Mazak Invests in Production Capacity, Future Workforce
Next year, Mazak will celebrate 40 years of manufacturing in Kentucky. In time for that anniversary, the company will complete the latest expansion of its Kentucky manufacturing facilities—an expansion that is currently underway, and that aims at increasing the production capacity at this site from 140 machines per month to as many as 200.

Mazak’s Discover 2013 event includes machine demonstrations and technical seminars in the company’s technology center (where this photo was taken), as well tours of the company’s Kentucky production operations.
Next year, Mazak will celebrate 40 years of manufacturing in Kentucky. In time for that anniversary, the company will complete the latest expansion of its Kentucky manufacturing facilities—an expansion that is currently underway, and that aims at increasing the production capacity at this site from 140 machines per month to as many as 200.
Those capacity figures are approximate, because they are affected by the mix of machine orders. More than 100 of the company’s machine models are produced at this plant. If the order mix shifts toward smaller machines, then more units per month can be produced. But that is not what’s happening right now, the company says. In part because of the aircraft industry, and in even larger part because of the oil and gas industry, Mazak has been seeing strong demand for many of its largest-size machines.
The company’s “Discover 2013” event, being held this week and next, offers visitors to the Kentucky facility the chance to see live machine demonstrations and participate in seminars on various topics in machining and manufacturing. Visitors to the event also have a chance to tour the company’s manufacturing operations.
In expanding those operations, the company faces a familiar challenge—familiar to both the machine tool maker and its customers. Namely, there is a relative scarcity of skilled manufacturing employees in the local labor pool.
In a speech yesterday at the company’s event, Mazak USA president Brian Papke said that manufacturers themselves ought to take a leading role in addressing this challenge. Together, they should provide for enough training opportunities that the pool of prospective manufacturing employees will grow.
The event this week was preceded by an outreach event in which the company opened its doors to more than 200 students from area high schools, as well as from Gateway Community & Technical College. Mazak partners with this institution, providing manufacturing students at the school with work-study opportunities aimed at skilled job positions with the company.
Mr. Papke, along with Ben Schawe, Mazak’s VP of manufacturing, described the effort and commitment necessary to provide for ongoing development of new manufacturing talent. Training has to be an expected part of the culture, they said. At Mazak, Gateway students are given assignments in various parts of the plant to help them find the work that suits them, and the students are assigned mentors who guide them in this exploration. The mentors take this role seriously, and the organization accepts that allowing some time to be spent in a seemingly unproductive way on young trainees is an important investment that will contribute in the long term not only to the company’s success, but also to the success of the manufacturing community overall.

To those who have toured the Kentucky plant before, a notable recent change is the increased use of robots for machine tending. On these machines making spindle components, a process formerly employing gantry loaders was replaced with a robot-fed process delivering greater throughput. The company routinely implements process improvements such as this not only for the sake of its own efficiencies, but also to develop an improved understanding of technologies offered to customers.

The plant is integrating machine tools into a plant-wide machine monitoring system taking advantage of MTConnect. Dashboards in the production area communicate machine utilization.
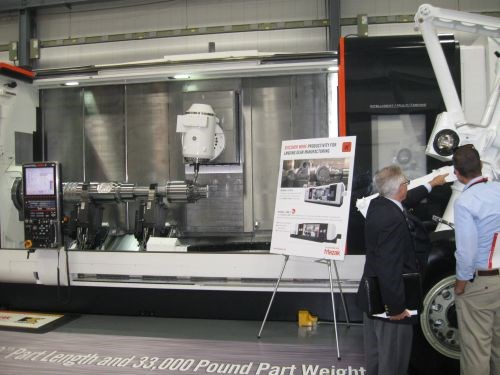
The company is seeing strong demand for large-scale offerings like this Integrex multitasking machine. Mazak displayed the machine alongside an aircraft landing gear.
Related Content
Can Connecting ERP to Machine Tool Monitoring Address the Workforce Challenge?
It can if RFID tags are added. Here is how this startup sees a local Internet of Things aiding CNC machine shops.
Read MoreAll-Around Mill Improves Productivity and Cost for Valve Job
Adopting a mill with a double-negative rake and pockets compatible with multiple insert geometries enabled Progressive Metal Service to increase feed and lower scrap rates for a valve.
Read MoreIf the Federal Government Is to Solve the Manufacturing Labor Shortage, it Needs to Start Here
Student-run businesses focused on technical training for the trades are taking root across the U.S. Can we — should we — leverage their regional successes into a nationwide platform?
Read MoreHow to Grow the Business with Real-Time Job Status Data
ERP systems that focus on making data more accessible can improve communication within a shop, reducing wasteful errors and improving capacity.
Read MoreRead Next
Seeing Is Believing: 3D Vision System Enables Bin-Picking Robot
With the help of a 3D vision system and robotic arms from FANUC, MetalQuest was able to automate a physically challenging bin-picking task.
Read MoreObscure CNC Features That Can Help (or Hurt) You
You cannot begin to take advantage of an available feature if you do not know it exists. Conversely, you will not know how to avoid CNC features that may be detrimental to your process.
Read More3 Mistakes That Cause CNC Programs to Fail
Despite enhancements to manufacturing technology, there are still issues today that can cause programs to fail. These failures can cause lost time, scrapped parts, damaged machines and even injured operators.
Read More