The automation market is growing rapidly, with affordable, space-saving robots and pre-engineered robotic work cells available for shops with tighter floor space limits and broader needs. From robot frames to racking systems, grippers, software and more, new automation technologies optimize workflow and deliver high consistency, efficiency and quality.
Today’s highly repeatable and flexible robots help to orient, produce and transport parts for both low-volume, high-mix and low-mix, high-volume shops. Tending, warehouse and secondary operations all see improvement from implementation of these robots, reducing costs and improving profits per square foot.
Tending Operations
Deploying robots for machine tending often improves throughput and operational safety while maximizing overall equipment effectiveness. Today’s robots also boast smaller space requirements, with compact and lightweight six-axis robots that can be mounted close to workpieces and machines in existing lines and cells. These types of robots are well-suited for extracting machined parts out of chucks and for loading mills. Robots with heavy-duty drive systems and higher vibration ratings extend this functionality to large parts.
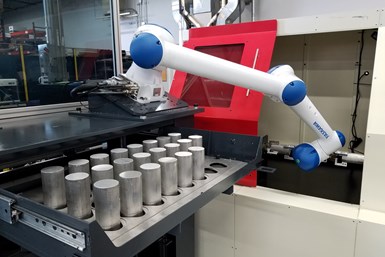
Robotic machine tending and part picking remain useful entry-level applications for automation. While they most benefit low-mix, high-volume shops, job shops with a wider variety of parts can also benefit from these robots with the right strategies. Photos courtesy of Yaskawa America, Inc.
Most modern machine tending robots boast repeatability under 0.1 mm, enabling them to outperform humans at highly mundane, repetitive tasks. These benefits extend beyond machining departments, too, with press brakes and horizontal injection molding machines (IMMs) also seeing performance gains.
Secondary Operations
The current wave of affordable, versatile robots has also affected secondary operations such as trimming, laser cutting, laser marking and deburring. Regarding the latter — whether a straight deburring or a hybrid deburring/polishing process is needed — both small and large parts with a variety of workpiece characteristics can be made assembly ready. Performing secondary tasks in the same footprint as primary operations further saves time and money.
Putting Peripherals Front and Center
Peripherals and other kinds of automated technology can improve the versatility and usability of robots. These can be included with the purchase of a robot, but in most cases, manufacturers should be able to retrofit peripherals into existing work cells.
Vision-guidance systems (VGR) simplify robotic programming, configuration and integration. The intelligent vision technology instructs the robot how to move and manipulate incoming workpieces, including those in different positions.
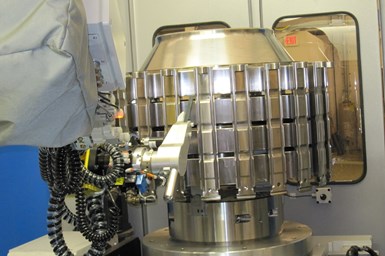
Automation goes far beyond machine tending — today’s robots can perform secondary operations such as laser marking and deburring in place. This increases the value of the work completed in the robot’s cell without requiring significantly more space.
Applications that demand a mobile robotic solution can turn to several options. A single robot on a traditional servo-track can still tackle large parts or applications where multiple machines need tending in succession, while autonomous mobile robots (AMRs) equipped with LiDAR sensors and other vision technology can meet a variety of other challenges. Capable of moving independently across the shop floor to their assigned tasks, AMRs simplify redeployments of industrial and collaborative robots to help with machine-tending tasks when having a dedicated robot is not practical. In certain applications, stationary robots designed to work collaboratively can load and unload items from AMRs.
Robotic integration can be easily managed via standard programming environments that eliminate the need for proprietary programming languages. Operators can simplify robot setup through motion control platforms or programmable logic controllers (PLCs), using these devices for wide variety of applications. For example, software interfaces can give a robot the ability to “know” the location of a specific product and act on that product as needed. Widely accepted Rockwell drives can be wired back to the PLC for position, speed and feedback information, giving the robot program the information required to track products along a conveyor and keep robots operating within their safe zones.
EuroMap 67-compliant electrical interfaces are hardware/software systems that streamline these tracking processes further. The best interfaces adhere to the Plastics Industry Association (PLASTICS)’s standards to transmit valuable information such as door status and robot operating and ejector position.
Factors to Consider
With a wealth of choices for robots comes a need to understand some of their ongoing developments. Weighing the features and needs of a particular robot will be valuable when considering what model of robot to purchase. Safety fencing requirements and the potential to leverage artificial intelligence are both important aspects of robots and robotic operations for consideration.
Depending on the application, safety fencing is not always required — collaborative robots often do not require fencing, and even some traditional industrial robots can operate without barriers. Some cases only require a safety device such as an area scanner or light curtain barrier. That said, for manufacturers mindful of their work cells’ total footprints, the use of safety fencing may actually be ideal even for collaborative applications. Depending on the option chosen, cycle time requirements should be considered, as robot speed is a factor for operator safety.
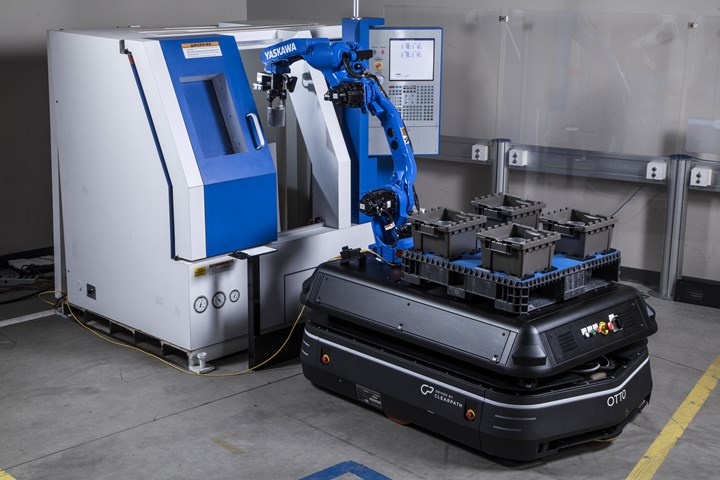
AMRs equipped with vision technology can not only serve as mobile tool carts and workpiece transport vehicles, these vehicles can easily redeploy industrial and collaborative robots across the shop floor to meet changing demands.
As for artificial intelligence (AI), strides in this field are facilitating safe, collaborative robot movement in three-dimensional environments, even when working with complex part varieties and shapes. AI also comes into play with AMRs, as these vehicles maneuver autonomously through facilities to perform specific tasks in a timely and safe manner, using mounted robots, vision systems, custom end-of-arm tooling and more to complete jobs.
Straightforward Robot Integration
When implemented in a smart, efficient way, robotic systems offer the potential for future success. While evolving customer requirements, supply chain challenges and skilled labor shortages will continue to reshape the industrial landscape, robots can alleviate many issues, elevating workforce productivity and maintaining fluid operations.
Related Content
Building a 5-Axis Cell
5-axis machining has taken over the metalworking industry, but what goes into a high-functioning 5-axis machining cell?
Read MoreLean Approach to Automated Machine Tending Delivers Quicker Paths to Success
Almost any shop can automate at least some of its production, even in low-volume, high-mix applications. The key to getting started is finding the simplest solutions that fit your requirements. It helps to work with an automation partner that understands your needs.
Read MoreBuilding an Automation Solution From the Ground Up
IMTS 2022 provides visitors the opportunity to meet with product experts to design automation solutions from scratch.
Read MorePartial Automation Inspires Full Cobot Overhaul
Targeting two-to-four hours of nightly automation enables high-mix manufacturer Wagner Machine to radically boost its productivity past a single shift.
Read MoreRead Next
Partial Automation Inspires Full Cobot Overhaul
Targeting two-to-four hours of nightly automation enables high-mix manufacturer Wagner Machine to radically boost its productivity past a single shift.
Read MoreCan Vision and Artificial Intelligence Make Every Robot Collaborative?
That is the aim of this Boston-area startup. Last year, it came to market with technology to make even fast and powerful industrial robots safe to approach. The technology promises to eliminate the need for guarding around them — safety measures that might not be as safe as you think.
Read MoreAutomating Material Handling Workflows With Autonomous Robots
Automation in a machine shop can boost throughput and productivity while easing the burden of the skilled labor shortage. Where do these self-guided mobile robots fit into the automation roadmap?
Read More