The biggest manufacturing event in North America, the International Manufacturing Technology Show (IMTS) returned to Chicago this month, drawing over 86,000 registered attendees. To report that the show this year was all about automation should come as no surprise — machining that is increasingly unattended is where production is headed and where it must go. And yet, to say that the number of robots and other part-handling automation systems throughout the show’s South Building this year is what made the show distinctive would not ring true. That is because the South Building (where machining centers, lathes and other chip-making machine tools are exhibited) had plenty of robots and part-handling systems on display back in 2018, the last time IMTS was held. Automation here is well-established. The major difference I noticed at IMTS this year was the extent to which exhibitors in other areas of the show — including the East and West Buildings highlighting tooling, workholding and inspection — now were also emphasizing solutions in support of unattended production.
Yet it must be said: The robots had a great show. Machine shops and other manufacturers seem to have widely accepted that labor will continue to be scarce, so they came to IMTS looking for solutions to let their existing talent oversee more production. A colleague of mine asked a representative of collaborative robot (cobot) maker Universal Robots just how well the show was going. Her response: “Oh my god! So good!”
But the impact of a robot can only reach so far. Other elements of the process also need to operate either seamlessly or quickly, or else the automation will be interrupted by a human needing to intervene. IMTS 2022 was the show in which suppliers serving various aspects of the machining process seemed to rise up together in recognition of this need. I saw at least five different facets of this, resulting in what I believe will be the first IMTS review I have written in which the developments I am citing occur largely outside of the machine tool exhibits of the show’s South Building. Here are the categories of technology advance that caught my attention this year:
1. Support for simulation of automated processes
Parts and equipment are too valuable and machining capacity is too much in demand for the validation of new machining processes to be done principally at the machine. Simulation software is the alternative, but it only works well if all the components of the process can be reliably modeled, tooling and workholding included.
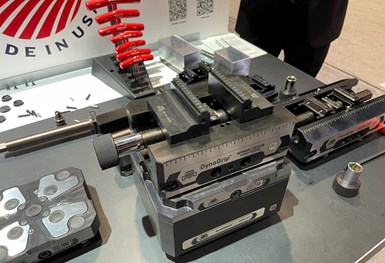
Mate Precision Technologies showed self-centering vises with a locking mechanism allowing for rapid and simple jaw change. The QR code visible on the vise links to (among other things) downloadable CAD files for modeling the vise accurately in offline simulation.
An example of a workholding provider recognizing this is Mate Precision Technologies. Precision vises from the company feature QR codes providing instant access not just to instructions and manufacturing information for that particular vise, but also downloadable CAD models of the vise usable in simulation.
Presetter data is potentially useful not just to the machine tool, but also to the simulation that proves out the process. This presetter system from Haimer provides a way to quickly scan the tool/toolholder assembly to obtain a model of it for use in simulation software.
Meanwhile, tool presetting technology provider Haimer now sees its systems not only serving the machine tools downstream with tool offset data, but also the digital simulation upstream that assures a reliable process. The company showed a presetting system that in two minutes performs a 3D scan to generate a model of tool and toolholder together for use in simulation.
Kawaski demonstrated a system in which robot paths can get better over time. Technology from Realtime Robotics compares programmed and actual robot movements, and refines programming based on this feedback.
Then there is the important extent to which even the physical process is a simulation that might yet yield clues to better performance. Kawasaki Robotics showed robots programmed via its open API by an AI system from Realtime Robotics. Among other things, Realtime’s software compares programmed robot movements to the robots’ actual joint angles to systematically update robot programming to create the most efficient paths possible producing the most precise robot motion.
2. Workhandling within the machine
This Unisig deep-hole drilling machine features integrated robotic handling. Long, slender parts such as bone taps can feature an OD profile with variable diameters and the need for holes of different IDs to meet within the part. The robot allows for pivoting and precision position to drill the part from both ends.
This one is not new, but I saw more sophisticated examples of it this year: adding to the axes of controllable motion inside the machining workzone by bringing in the device that can move or position the part. Unisig showed this idea applied to deep hole drilling; a machine able to produce precision bone taps features an internal robot for pivoting the part so it can be drilled from each end. Meanwhile, SMW Autoblok, through a mechatronics group the company has launched, offered a view of just how much more standard workholding such as a lathe chuck might be able to do. Its chuck designs with independently controllable jaw movements allow for precise and automatic centering of round parts, as well as precise positioning of non-round parts in need of turning operations.
3. Swiss going global as a platform for unattended production
Mazak's Syncrex Swiss-type machine features both a sliding door and a folding overhead door to maximize the operator's access to the workzone. It also features what the company calls its High Damping Composite Casting base for precision through rigidity and vibration control.
An unattended machining process able to run effectively lights-out has to begin with precise and efficient setup while the lights are still on. Iscar's quick-change Swiss tooling features a precision locking geometry that can be seen here.
CNC Swiss-type lathes are no longer the equipment of specialty turning houses; this platform is now also widely accessible and usable by job shops with broader ranges of equipment. Machine tool maker Mazak recognizes as much — this year saw the IMTS debut of its Syncrex line of CNC Swiss-type machines. One of the major factors driving Swiss adoption is the extent to which a bar-fed Swiss-type machine is a productive, reliable system for unattended production.
The modular quick-change Swiss-type tooling system seen here from Tungaloy supports through-holder coolant rated to 2,000 psi.
The greater emphasis on Swiss was evident throughout the tooling pavilion of the show. Various cutting tool makers showed new or updated offerings in quick-change modular tooling for Swiss-types. Other exhibitors aimed at extending these machines’ capabilities. One example: Pilot Precision showed a new version of its broaching head driven by the rotary-tool spindle of a live-tool lathe, now scaled down to fit within the work envelope of Swiss-types.
4. Digital support for maintenance
Robotic part handling is fascinating to watch, but could we also get a hand for some of the more mundane aspects of keeping a machining process running?
Coolant handling deserves automation, too. Jorgensen showed a coolant system that comes close to being hands-free. Cyclonic filtration eliminates filter media. Closed-loop monitoring maintains both the coolant's level and its concentration.
Coolant handling equipment provider Jorgensen showed digital technology aimed at automating what one representative called “the two most miserable people in the shop” — namely, the operator topping off coolant and the technician cleaning coolant hardware. The company’s cyclone-filtering self-monitoring coolant system both eliminates filtering media and senses coolant condition to automatically keep coolant level and concentration on target.
For maintenance needs that are less routine, grinding machine maker Star Cutter debuted its Augmented Reality Support Service. Two-way augmented reality glasses are sent to customers so that service specialists can see precisely what machine users are seeing, and can guide them in making adjustments or repairs by circling, highlighting or drawing arrows within the glasses-wearer’s field of view. The aim is to provide a fast return to machine uptime by eliminating the need to wait for a service specialist to travel to the shop.
5. Inspection as an automation enabler
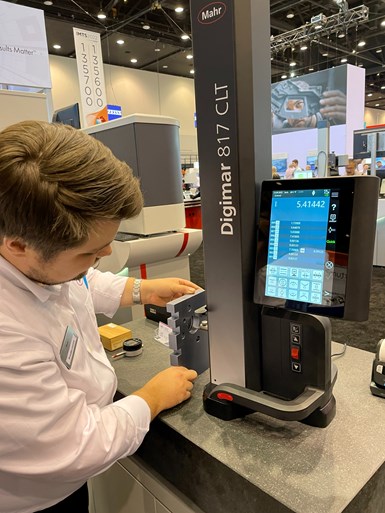
Mahr demonstrated a height gaging allowing for accurate gaging with little training. The system captures and logs intended measurements in response to simple moves from the user.
The potential downfall of any automated process is that uncontrolled variables might allow the precision of the process to drift, or that parts might pile up waiting for measurement to validate them. Innovations in the quality-assurance pavilion of the show tended toward not just automation but also rapid ease of use as a means of supporting unattended production.
Gage with each grab. New Scale Robotics integrates calipers into robot grippers, making measurement a seamless element of part handling.
In the latter category, Mahr showed a height gage system allowing for fine measurement with quick motions by the operator. The system anticipates it will be making a measurement when the user simply presses its arm down, then uses sensing to find and stop at the feature measured while logging and compiling measurements automatically — all to allow an operator to measure quickly and reliably without methodical steps or detailed training.
Meanwhile, maybe my favorite product introduction of the show (because it is so practical) was displayed by New Scale Robotics. The company offers cobot grippers with integrated caliper gaging — meaning the robot can gage a part each time it grabs a part. In one machine shop that uses this system to tend an automated lathe, the company says the robot confirms part OD as a consequence of unloading each part. If the diameter ever trends out of spec, the robot simply raises its arm to signal to the shop that attention is needed.
Peter Zelinski writes about manufacturing technology and how it is changing. Find more of his work related to CNC machining and additive manufacturing. To suggest an article topic related to a success in your manufacturing facility or business, or a technology development you are close to, email him here.
Related Content
STLE Opens Registration for 2024 Annual Meeting
The Society of Tribologists and Lubrication Engineers’ 2024 STLE Annual Meeting & Exhibition will take place May 19-23 at the Minneapolis Convention Center in Minneapolis, Minnesota.
Read MoreSTLE To Host Metalworking Fluid Management Program
STLE’s program is a two-and-a-half-day education program offering a comprehensive overview of metalworking fluid management.
Read MoreHennig Inc. Acquires Industrial Coolant Systems
ICS develops and field tests high-pressure coolant systems, coolant filtration systems and other machine tool solutions.
Read MoreManaging Coolant with Skimmers, Refractometers and More
Bacteria-infected coolant harms machines and sickens machinists. Coolant management technologies like skimmers and automated systems counter this tendency.
Read MoreRead Next
3 Mistakes That Cause CNC Programs to Fail
Despite enhancements to manufacturing technology, there are still issues today that can cause programs to fail. These failures can cause lost time, scrapped parts, damaged machines and even injured operators.
Read MoreThe Cut Scene: The Finer Details of Large-Format Machining
Small details and features can have an outsized impact on large parts, such as Barbco’s collapsible utility drill head.
Read More