Lean Approach to Automated Machine Tending Delivers Quicker Paths to Success
Sponsored ContentAlmost any shop can automate at least some of its production, even in low-volume, high-mix applications. The key to getting started is finding the simplest solutions that fit your requirements. It helps to work with an automation partner that understands your needs.
Share
Read Next
By SCHUNK
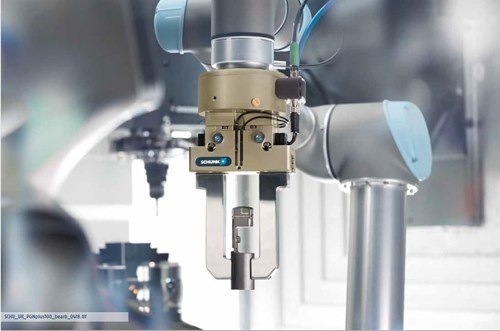
Most shops these days need some form of automation. It’s not just about the lack of skilled labor. For the sake of pure competitiveness, shops need to find ways to reap the best utilization of their people and equipment to maximize throughput and enable growth. What worries many shop owners is how to deal with the apparent complexity and uncertain return that could come from an automation project.
Taking a lean approach to automation lowers the financial risk and time involved in implementing successful automation projects. Start by addressing opportunities for improvement with the simplest solutions available. You’ll be able to generate real ROI quickly. As confidence grows, a shop can move on to more complex systems. But regardless of the application, always look for the simplest approach that fits your specific needs.
It’s important to recognize that machine tending automation is not just about robots, though they may be appropriate in many applications. The challenge is how to keep the machine running more hours of the day. Workpiece complexity or variance, lot size, available budget and experience will be important factors in choosing a solution that makes sense, and that makes money. Automated part load/unload is usually part of that scenario, but other enabling technologies such as flexible workholding and part gripping solutions also play vital roles. These are key to making automation cost effective particularly in low volume, high mix applications.
SCHUNK has been engineering automation projects for years and contributes to those solutions with a wide range of workpiece holding and handing equipment. Here's SCHUNK’s overview of automation solutions that could be a relatively easy lift for any shop to get more production out of their existing equipment.
A Quick Path to Robotic Loading/Unloading
While robotic machine loading/unloading may seem a daunting challenge, there is a great way to start that is relatively simple to implement, not very expensive, and can work with your existing equipment. Standard component packages are available that enable the implementation of cobots with seamless integration at a level almost any shop can master. This is facilitated by cooperation between cobot/robot manufacturers and component suppliers, as well as advancements in the software and user interface design.
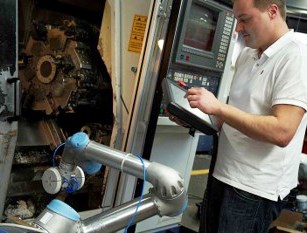
Cobots are relatively easy to deploy and can tend almost any kind of machine tool.
Cobots – which stands for cooperative robots – present a much more friendly environment to do machine tending for shops new to this sort of automation. Cobots are generally less expensive than industrial robots and easier to program. As the name implies, they can work in close quarters with shop workers because they have sensors that immediately shut down movement when unexpected contact is made with any obstacle, such as a machine operator, so that safety fences are not required. They are also very space efficient and easy to redeploy for other jobs or on other equipment.
Compared to more complex automation systems, cobots are inherently easier to work with in general due to the focus on user interaction and interoperability with other hardware. Moreover, component suppliers like SCHUNK have developed software and communication protocols that allow system components to be more easily recognized by the cobot control software.
Direct robot loading which will also require a gripper and automated clamping system can still be quite flexible, and is usually applied when dealing with lot sizes that are a bit larger, like 50 pieces or more. Robots also can accomplish more than just machine tending, for example, to integrate a gaging stand into the system. In some cases, secondary operations such as deburring can be handled as well.
Flexible End-of-Arm Tooling is Key
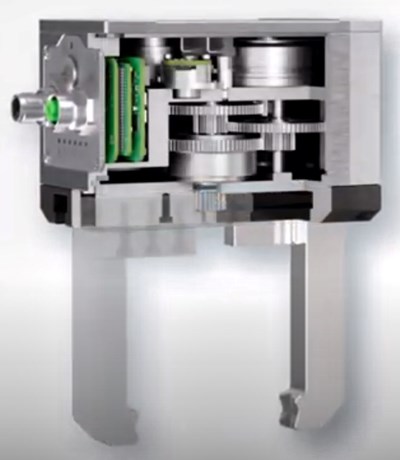
SCHUNK’s EGU/EGK grippers have a self-contained servo motor that actuates the gripping fingers.
A key to making robotic machine tending more flexible is the availability of end-of-arm tooling that is simpler to use and faster to change over from job to job. For example, SCHUNK’s EGU/EGK grippers have a self-contained servo motor that actuates the gripping fingers. This enables the unit to have a large but precisely controlled gripping range which can often accommodate different parts with just a simple programming adjustment. The servo system includes an absolute encoder so that finger position is always referenced. It allows the fingers to be pre-positioned at high speed and gripping force can easily adjusted for any given part. Changeover is quick and simple which makes the grippers extremely flexible, particularly for shops that do a lot of setups.
A great example of this is SCHUNK’s machine tending bundle that includes a gripper solution, workholding solution, and valve block that makes controls easy to set up. There are standard plug-ins for most all cobot/robot manufacturers which makes the programming simple to execute.
Flexible, Pre-packaged Industrial Solutions for Automated Machine Tending
A number of machine tool manufacturers now have standard “bolt-on” automation options that can be added directly to a machine to provide some form of automated machine tending. There are also a number of 3rd party machine-agnostic providers that can automate your existing equipment. A few great examples include Trinity Automation, Fusion OEM (Robojob), and Gosiger AWR.
Some of these solutions use standard pallet storage systems where jobs are set up offline on a pallet, loaded into the store, and then automatically loaded onto the machine at the appropriate time. Others are based on direct robot loading/unloading.
Pallet storage solutions are ideal for low lot sizes and high-complexity parts. Here workholding setups are built offline on precision pallets and then loaded into a multi-pallet load/unload system. They can even efficiently produce single-piece lot sizes since a pallet is being loaded instead of the workpiece. This enables the use of a wide variety of workholding solutions that can be as complex as required. Once the workholder position on the pallet is known, new setups can be loaded on the machine in seconds as long as the machine is appropriately tooled for the job. This enables machining on demand – a growing demand for contract shops – as well as hours of unattended machining for almost any kind of part.
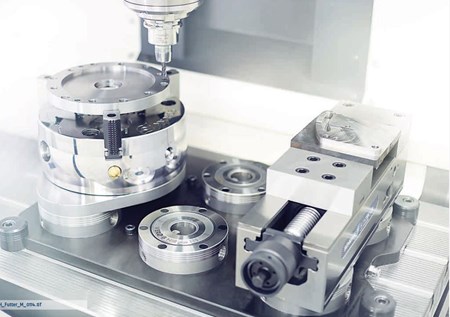
Quick-change pallet systems are a key enabler to flexibility in automation systems. They allow workpiece location to be established quickly and reliably, and facilitate rapid setup of new jobs.
Another critical aspect of achieving success with prepackaged systems is having software that is flexible and easy to use. If you’re machining thousands of parts in a run, you can afford to engineer more dedicated gripping solutions. But in higher mix environments it’s important to have an interface that is easy for operators to understand and that can be adjusted in minutes rather than hours, just like you’d expect of your CNC machines.
Turnkey Solutions
Many applications could warrant the outsourcing of a turn-key solution where the provider studies your parts and throughput requirements to deliver the entire system functioning as planned. With turnkey systems the possibilities are endless. They are ideal when the investment and commitment are justified by the length of the contract or program. Turnkey solutions can also be flexible. For example, utilizing more flexible end effector tooling as discussed above, systems can be designed to accommodate families of parts that are readily adaptable to changing demand volumes and mixes.
Solutions can be applied to advanced machine technology like multitasking machines, even using pallet storage systems for low lot sizes. Lathe chucks can be used with integrated hydraulic cylinders in turning applications and with pallet storage as well. Workholding can be used with automatic jaw-change technology which accommodates workpiece changeover without operator intervention.
The same goes for grippers. By using an automatic gripper-changing system a robot can be equipped to handle workpieces of all shapes and sizes.
You’re Not Alone
But most shops starting out with automation will be well served to focus on far simpler applications at first to begin reaping the benefits of better utilization of equipment and personnel. The good news is that automation on this level doesn’t have to be unduly difficult or expensive, even in low-volume, high-mix production environments. To stay competitive, the key is to get started with the low-hanging fruit and then you can discover how much automation really makes sense for your business.
For most people, the hardest part of automation is getting started. It is here that it pays to work with professionals who understand all the options, opportunities and pitfalls of bringing new forms of automation to a shop. No one is going to understand your parts better than you do, but a good partner will augment that knowledge with the expertise to design an automation system that brings real value to your existing shop environment. No one vendor has all the answers. The good news is that an ecosystem of automation components has developed that makes integration easier and faster than ever before. The key is finding an automation partner that will help you fit all the pieces together in a way that best fits your shop’s needs.
For more information on automation solutions, please visit SCHUNK.com.