Turning Tools
Turning involves a fixed and non-rotating cutter, because in turning, the workpiece spins instead of the tool. Turning tools typically consist of a replaceable insert in a turning tool body. The insert can be distinctive in a number of ways, including shape, material, coating and geometry. The shape can be round to maximize edge strength, diamond-shaped to allow a sharp point to cut fine features, square, or even octagonal to increase the number of separate edges that can be applied as one edge after another wears out. The material is typically carbide, though ceramic, cermet or diamond inserts can be applied to more demanding applications. A variety of protective coatings also help these insert materials cut faster and last longer.
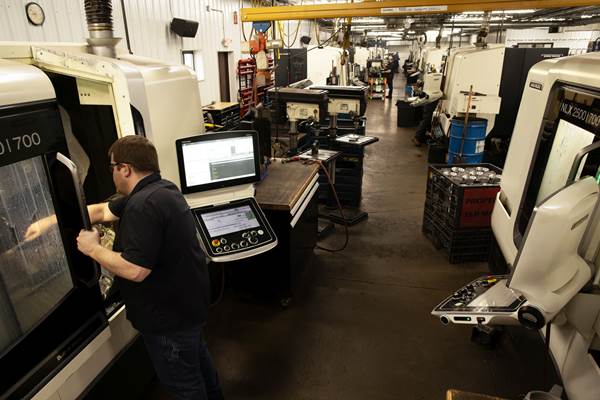
ESSENTIAL READING
VIEW ALLHow to Turn Machine Shop Downtime Into Process Expertise
To take advantage of a lull in business, JR Machine devised a week-long cutting tool event that elevated the shop’s capabilities with aerospace alloys.
Read MoreBuying a Lathe: The Basics
Lathes represent some of the oldest machining technology, but it’s still helpful to remember the basics when considering the purchase of a new turning machine.
Read MoreChoosing Your Carbide Grade: A Guide
Without an international standard for designating carbide grades or application ranges, users must rely on relative judgments and background knowledge for success.
Read MoreMachining 101: What is Turning?
Turning uses a lathe to remove material from the outside of a rotating workpiece, while boring does the same from the inside of a rotating workpiece.
Read MoreWhy Binderless CBN Inserts Turn Titanium Faster
A new formulation of cubic boron nitride could provide a more solid alternative to cemented carbide as finish-machining becomes more demanding.
Read MoreCutting Tool Technology Aids Lights-Out Machining Applications
These features can help improve cutting tool stability, standardize cutting performance and extend tool life, enabling shops to confidently run unattended shifts.
Read MoreLatest Turning Tools News And Updates
Allied Machine's Threaded Lathe Sleeves Maximize Coolant Flow
The sleeves are well suited for job shops that are using aging lathes, and are designed for use on machines that do not have the capability to run through-the-turret coolant.
Read MoreTungaloy Grooving Toolholders Provide Highly Stable Machining
TungHeavyGroove includes an enhanced insert clamping design for maximum tool rigidity.
Read MoreSeco Tooling Lineup Promotes Optimized Part Processing
The company’s expanded tooling lineup is aimed at applications ranging from general ISO turning to high-volume hard turning and deep-hole drilling.
Read MoreTungaloy-NTK Swiss Turning System Provides High Repeatability
The ModuMiniTurn modular turning tool system provides exceptional repeating accuracy for the cutting point when swapping out modular heads for new inserts.
Read MorePlatinum Tooling Becomes Distributor for Rev Broaching Tools
Rev S.R.L.’s broaching solutions for CNC lathes and machining centers are said to be ideal for machining simple keyways or internal and external profiles, both teeth and splines.
Read MoreKyocera Precision Tools' Coated Carbide Optimizes Turning
The CA115P/CA125 series is designed to provide extended tool life and superior performance in a variety of machining scenarios.
Read MoreFeatured Posts
Buying a Lathe: The Basics
Lathes represent some of the oldest machining technology, but it’s still helpful to remember the basics when considering the purchase of a new turning machine.
Read MoreChoosing Your Carbide Grade: A Guide
Without an international standard for designating carbide grades or application ranges, users must rely on relative judgments and background knowledge for success.
Read MoreLive Tool Speed Increaser Spurs Engraving Cost Savings
By using a Heimatec speed increaser provided by Platinum Tooling, Kurt Machining was able to achieve ninefold cost savings for a project engraving 6060 aluminum.
Read MoreMachining 101: What is Turning?
Turning uses a lathe to remove material from the outside of a rotating workpiece, while boring does the same from the inside of a rotating workpiece.
Read MoreShifting Toward Preparedness and Flexibility with Turning Tool for Steel
The pandemic has taught manufacturers to reevaluate their preparedness for unexpected and drastic market disruptions. A practical example from a cutting tool manufacturer may show the way.
Read MoreWhy Binderless CBN Inserts Turn Titanium Faster
A new formulation of cubic boron nitride could provide a more solid alternative to cemented carbide as finish-machining becomes more demanding.
Read MoreFAQ: Turning Tools
What is turning?
Turning is the process of using lathes to remove material from the outer diameter of a rotating workpiece. Single-point tools shear metal from the workpiece in (ideally) short, distinct, easily recyclable chips.
Source: Machining 101: What is Turning?
How do you sharpen turning tools?
Early turning tools were solid, rectangular pieces of high-speed steel with rake and clearance angles on one end. When the tool dulled, machinists would sharpen it on a pedestal grinder for reuse. High-speed steel tools are still common on older turning machines, but carbide has become more popular, especially in brazed single-point form. Carbide sports better wear resistance and hardness, leading to better productivity and tool life, but it is more expensive and requires expertise to resharpen.
Source: Machining 101: What is Turning?
What is cutting feed and speed?
Turning is a combination of linear (tool) and rotational (workpiece) movement. Thus, cutting speed is defined as the rotational distance (recorded as sfm — surface feet per minute — or smm — square meters per minute — traveled in one minute by a point on the part surface). Feed rate (recorded in inches or millimeters per revolution) is the linear distance that the tool travels along or across a workpiece surface. Feed is also sometimes expressed as the linear distance the tool travels in a single minute (in./min or mm/min).
Feed rate requirements vary depending on the operation’s purpose. In roughing, for example, high feeds are generally better for maximizing metal removal rates, but require high part rigidity and machine power. Finish turning, meanwhile, might slow down the feed rate to produce the surface finish specified on the part blueprint.
Source: Machining 101: What is Turning?
What is boring?
Boring is primarily used for finishing large, cored holes in castings or pierced holes in forgings. Most tools are similar to those in traditional, external turning, but cutting angles are particularly critical due to chip flow concerns.
Source: Machining 101: What is Turning?
What is a spindle?
The spindle on a turning center is either belt-driven or direct-drive. Generally, belt-driven spindles represent older technology. They speed up and slow down at a lower rate than direct-drive spindles, which means cycle times can be longer. If you’re turning small-diameter parts, the time it takes to ramp the spindle from 0 to 6,000 rpm is significant. In fact, it might take twice as long to reach this speed than with a direct-drive spindle.
A small degree of positional inaccuracy may occur with belt-driven spindles, because the belt between the drive and the positional encoders creates a lag. With integral direct-drive spindles, this is not the case. Ramping up and down with a direct drive-spindle happens at a high rate, and the positional accuracy also is high, a significant benefit when using C-axis travel on live-tooling machines.
What is the function of a tailstock on a lathe machine?
A built-in, numerically controlled tailstock can be a valuable feature for automated processes. A fully programmable tailstock provides more rigidity and thermal stability. However, the tailstock casting adds weight to the machine.
There are two basic types of programmable tailstocks — servo-driven and hydraulic. Servo-driven tailstocks are convenient, but the weight they can hold may be limited. Typically, a hydraulic tailstock has a retractable quill with a 6-inch stroke. The quill also can be extended to support a heavy workpiece, and do so with more force than a servo-driven tailstock can apply.
Turning Tools Supplier Categories
- Tap Drivers & Attachments
- Tool Presetters
- Ceramics
- Tooling Materials, Ceramics
- Drills
- Drill Bushings
- Diamond Tools
- Spline Inserts
- Boring Tools
- Gear Cutting Tools
- End Turning Machines
- Cut-Off Tools/Attachments
- Grooving Tools
- Tool Repair, Coating & Treatment Services
- Tooling Materials, Carbides
- Carbides
- Broaching Tools
- Slotting Saws
- Horizontal CNC Turning
- Tool Blanks
- Burnishing Tools (Roller)
- CNC Turn/Mill Machines
- Tool Conditioning Equipment
- Honing & Lapping Tools
- Serration Tooling
- Tool Condition Monitoring Systems
- Tool Storage & Handling Systems
- Lathes, Cycle-Controlled (Semi-CNC or "Teachable")
- Cut-off Lathes
- Twin-Spindle/Twin-Turret Turning
- Saw Blades
- Arbors (for Cutters)
- Vertical CNC Turning Centers
- Counterbores/Countersinks
- Manual Lathes
- Shaving Tools
- Boring Tools for Turning Machines
- Reamers
- Tooling Systems, Modular and/or Quick-Change
- Drill Chucks
- Toolholders
- Chamfering Tools
- Inverted Vertical CNC Turning