CAM's Simulation Capability Boosts OEM's Spindle Uptime
CAMWorks and CAMWorks ShopFloor have boosted Anchor Danly’s spindle uptime by 15-20% through simulation and automatic G code updates.
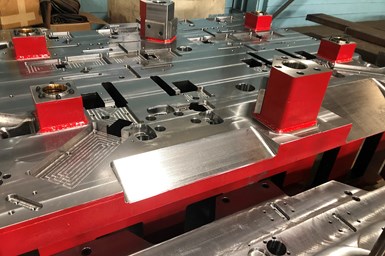
Anchor Danly creates die sets, components, steel plates and metal fabrications for a wide variety of industries and applications. Serving all of its customers requires the productivity achieved through an efficient CAM solution.
Photo Credit: CAMWorks
Anchor Danly is an international manufacturer and distributor of die sets, components, steel plates and metal fabrications. Their products are used in machine bases; tools, dies and molds for metal working and injection molding; mining and construction equipment. With four facilities in Canada and the United States, Anchor Danly is the original equipment manufacturer (OEM) and distributor of the Danly: Lempco & Anchor style die set. In addition to producing these products, the company serves as a distributor for the Danly-IEM, Lamina, Lempco and Special Springs nitrogen lines of tools and mold components. The automotive industry constitutes Anchor Danly’s largest single custom metal parts market, but the manufacturer also serves markets from automation to agricultural equipment to aircraft.
According to Anchor Danly’s customer service and process manager Ryan Wozniak, using an efficient, integrated CAM package is critical for achieving the productivity gains that the manufacturer needs to continue to grow and be successful.
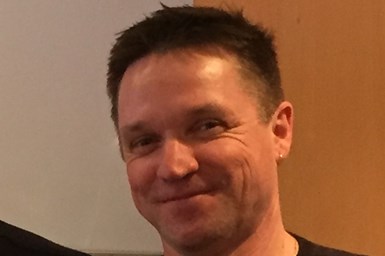
Anchor Danly customer service and process manager Ryan Wozniak says that CAMWorks ShopFloor handily meets Anchor Danly’s needs, increasing spindle uptime, improving estimate accuracy, automatically updating G code and replacing paper reference documents.
Photo Credit: CAMWorks
Choosing the Right CAM
While Anchor Danly had used CAM software before 2005, it was around this time that “management actively sought something that would improve G code programming consistency, boost productivity, improve quality, and facilitate more accurate estimating and quoting,” Wozniak says. “We were impressed with CAMWorks because of the automatic feature recognition capabilities and technology database.”
In the spirit of continuous improvement, Anchor Danly recently conducted another investigation into CAM systems to see if other systems better met the manufacturer’s needs. Wozniak says this investigation “confirmed that CAMWorks — and the CAMWorks ShopFloor application that we’ve since implemented — is the best solution for helping us cut metal quickly and accurately.” Adding weight to that confirmation was the mid-investigation announcement that CAMWorks had fully integrated with Solidworks CAD software.
Uptime and G Code Improvements
Using CAMWorks milling and CAMWorks ShopFloor measurement, cross-sectioning and machining simulation capabilities, Anchor Danly has been able to increase spindle uptime while simultaneously improving quality and reducing scrap and rework.
“CAMWorks ShopFloor helps our operators work smarter, not harder,” Wozniak says, “enabling us to increase throughput and keep the spindles turning.”
“From the way that CAMWorks works hand-in-hand with Solidworks CAD software to the ability to simulate tool paths and access sub-routines from the technology database, CAMWorks has helped us to improve our quality and increase spindle uptime, which is up at least 15 to 20%,” Wozniak says. “We’re not wasting time re-programming or dealing with inconsistency in the G code we’re running, because it’s all in the database.”
Simulating for Confidence
With the combination of CAMWorks and CAMWorks ShopFloor solutions, Anchor Danly has not only improved its estimating and quoting accuracy but also increased the confidence of machine operators. This results in less down time, because machine operators now have tools to interrogate 3D Solidworks models directly and update G code automatically to match design changes, as well as tap existing G code in the technology database for common and complex operations.
“With CAMWorks ShopFloor, there’s greater ease of understanding about what’s going on among the operators,” Wozniak says. “Every mill has a 60-inch monitor on which operators can view the 3D solid model, measure features, cross-section them and simulate the entire toolpath. In addition to helping our mill operators, the ability to simulate an entire milling operation in CAMWorks has helped our estimators become more accurate with quoting complex work because they can take the time calculated by the simulation, add a plus factor for bio breaks and tool changes and then produce a very accurate quote.”
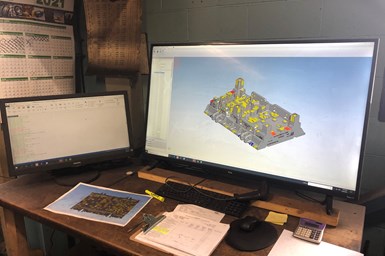
To leverage CAMWorks’ Solidworks integration and CAMWorks ShopFloor’s simulation abilities, every mill at Anchor Danly has an associated 60-inch monitor for viewing a 3D model of the part undergoing manufacturing.
Photo Credit: CAMWorks
No More Paper
In addition to increasing machine up-time, boosting quality and improving quoting accuracy, the combination of CAMWorks and CAMWorks ShopFloor solutions has allowed Anchor Danly to implement a completely paperless system — with monitors on the shop floor digitally representing all drawings, setup sheets, shop prints, tool lists, models and machining processes. This digital system has enabled the company to completely eliminate paper and printing costs from its operations.
“We used to print off 50-page prints for every milling operation for reference by our operators and then throw them away once the operations were complete,” Wozniak explains. “Although it took some time to adjust to the change, now there is an appreciation for having easy and quick access to all of the information about each job — from the 3D model to the machining simulation to all related information. CAMWorks ShopFloor helps our operators work smarter, not harder, enabling us to increase throughput and keep the spindles turning.”
Related Content
5 Tips for Running a Profitable Aerospace Shop
Aerospace machining is a demanding and competitive sector of manufacturing, but this shop demonstrates five ways to find aerospace success.
Read MoreWhen Handing Down the Family Machine Shop is as Complex as a Swiss-Turned Part
The transition into Swiss-type machining at Deking Screw Products required more than just a shift in production operations. It required a new mindset and a new way of running the family-owned business. Hardest of all, it required that one generation let go, and allow a new one to step in.
Read MoreShop Quotes Smarter, Works Harder with Machine Monitoring
Temco first installed MT-LINKi to optimize quoting. Now, the software helps the shop optimize its machines — and machine purchases.
Read MoreIncrease Savings and Streamline Purchasing Operations with Amazon Business
Machine shops and small manufacturers are finding cost and time savings using Amazon Business in their shops.
Read MoreRead Next
Let’s Finish Closing the Quoting Gap
Sharing accurate, timely and actionable data is the key to an effective, respectful relationship between a machining job shop and the subcontracting finishing shop. Software that streamlines the quoting process can make this happen.
Read MoreFour Keys to Establish a Digital, Paperless CNC Machine Shop
Paperless digital workspaces can help CNC machine shops save money and improve workflow through improved internal connectivity, but getting there requires the right tools and careful strategies.
Read MoreIntegrated CAM Software Automates Data Transition From Engineering to Production
By switching to CAMWorks software, Decimal Engineering was able to boost its throughput and quality while saving time and money.
Read More