Finally, A Comprehensive Software Solution Designed for Small Job Shops
Sponsored ContentZel X from Siemens is an integrated software application that consolidates collaboration, design, manufacturing, and operations into a comprehensive, easy-to-use solution. From RFQ to delivery, it’s a more efficient way to handle quotes, manage jobs, make parts, and collaborate with teams of all sizes.
Share
You run a small job shop and you do everything. Work with customers. Quote. Schedule and run jobs through the shop. Maybe design a fixture from time to time or run a part. There is specialized software for all these tasks, but they are overkill for your needs, complicated to learn, and often expensive. Who has the time or money for that?
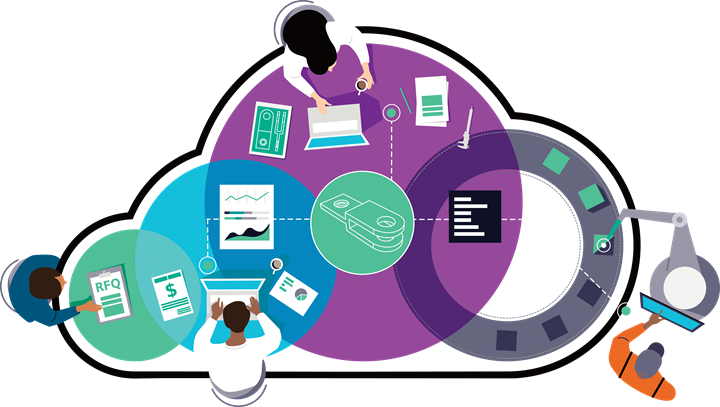
Zel X brings key job shop functions together in a single easy-to-use suite of applications.
Finally, there is software designed to give small job shops just what they need to run all aspects of the business in a single integrated easy-to-learn application. It facilitates job quoting and management, collaboration with customers and employees and even includes CAD and CAM. It allows you to work with customers the way they want to, manage the shop the way you want to, and not get bogged down with complex software functionality you’ll never use. And because it’s cloud-based, you won’t need IT support to use it.
The application is called Zel X and it is provided by Siemens Digital Industries Software. If you think of Siemens as a high-end software developer, that’s right, they are. But with Zel X, Siemens exhaustively studied how small job shops really work and brought just the level of these technologies that shops really use. This improves the utility of the system, reduces the training required to use it, and gets you beyond running the business with spreadsheets, marked up PDFs, emails and other forms of manual documentation. It brings everything you need for a job together into a single, easily accessible project folder.
What’s Included in Zel X
Every shop has essentially the same process for doing a job. You get an RFQ, cost and quote it, document job requirements, get a part program, and send it all to the shop. The problem is when the job information resides in different places. Did the customer send a CAD file or just a drawing? Where is it? What machine(s) do I need and are they available? Do we have material? The customer just sent changes; where are we on the job?
Dealing with any of one these things is not difficult on its own. It’s the confusion of dealing with it all at once that’s the trick, particularly when you don’t have all the necessary information at your fingertips. This is what Zel X addresses. With a single application you can:
-
Zel X enables paperless collaboration with internal teams and customers.
- View and markup all associated files on any device
- Create and validate a CAM part program
- Build an electronic part file from a print or design fixturing and other tooling
- Store quality requirements
- Build a task-based router and track job progress
Each time a new piece of information is obtained (CAD files, customer emails, etc.) or created it is added to the job folder in a structured manner and made instantly accessible to all the people who need to know. All this data is stored in a cloud-based server that is accessible via browser on any device. Generally, very little training is required to use Zel X, though web-based tutorials are available. You just download the app and start using it.
More On Each Zel X Capability Area
Zel X includes four primary capability areas which help manage almost any aspect of a job shop business. They are:
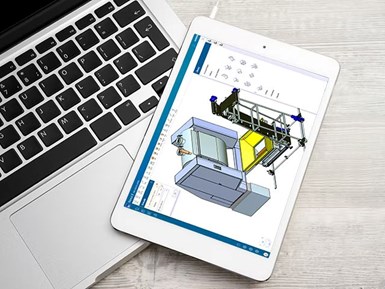
Visualization tools provide easy to understand graphical depictions of parts, equipment, setups and more.
Collaboration – The collaboration capabilities bring teams and supply chains together with secure online project file sharing and cloud storage. This includes:
- Permission-based file sharing
- Task management
- Mobile CAD review
- Phone/tablet CAD augmented reality (AR)
- Mobile review of multiple file types (PDF, XLSX, image, etc.)
Operations – The operations capabilities provide shop management tools designed specifically for smaller job shops. It includes
- Quote tracking
- Digital traveler/shop floor tracking
- Customer RFQ handling
- Sub-contractor/supplier RFQ management
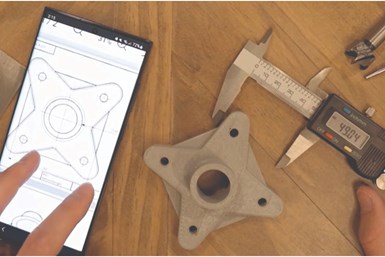
Browser-based access enables mobile-assisted inspection and many other functions.
Manufacturing – The manufacturing capabilities include 2.5 axis CAM based on best-in-class technology to make the most of your machine investments:
- CAM for quote estimates
- CAM for CNC toolpath generation
- Mobile inspection for first article validation
Design – The design capabilities provide easy-to-use design and modeling tools to help with quote generation, manufacturability improvements, CNC preparation, fixture design, collaboration and more. Important features include:
- Shape library for starting quickly with pre-set forms
- Rapid direct editing
- Multi-body models for assembly mock-up
- Automated critical dimension drawings
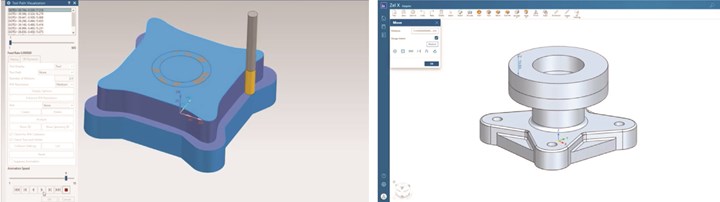
Simplified CAD and CAM functions enable part models to be created quickly to be used for job estimation or 2.5-axis programming.
How Zel X Works
Because Zel X is cloud-based it requires no internal IT infrastructure to deploy and is accessible by any internet-connected device. It requires no massive downloads or lengthy installations, and continual software updates are provided as part of the package. Rather than making a capital purchase to buy the software, it is accessed inexpensively with an annual subscription fee of $1,296.
Siemens also offers a one-month free trial that includes fully licensed software with guided tutorials. You can sign up with a valid email address, LinkedIn profile, or Google login. Or, use this code for a 50% discount on your first year subscription: MMSHALF.
There simply is no easier or less expensive way to get started in digital manufacturing management that is capable of being tailored to your preferred business practices. That will help make the shop more efficient and profitable while better serving customers.
Please visit the website to learn more about Zel X from Siemens.
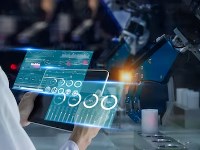
White Paper
Six Reasons to Automate Your Job Shop Office
How to improve profitability and support growth with automation