Selecting a Thread Mill That Matches Your Needs
Sponsored ContentThreading tools with the flexibility to thread a broad variety of holes provide the agility many shops need to stay competitive. They may be the only solution for many difficult materials.
Share

Historically, the threading of holes has been a fairly straightforward operation, usually performed close to the end of a part’s machining. Once the holes had been drilled, thread taps of the appropriate sizes would be used to efficiently and effectively thread them.
In some instances, this old-school approach still provides exceptional results. For shops producing a high quantity of identical holes in relatively soft materials, thread taps are hard to beat. Yet, technological advances in a variety of areas have created a host of situations ill-suited to the traditional approach, as well as improved solutions for tackling them.
For example, materials that are some combination of hard, exotic and difficult-to-machine have transformed the landscape. Not only are these materials more challenging to work with, but their higher price significantly increases the cost of scrap. For a small or mid-size shop, a broken tap in a large, nearly finished part can do substantial harm to the month’s profitability. A broken thread mill, on the other hand, can easily be removed and is unlikely to significantly damage a part.
Additionally, between the shift toward smaller lot sizes and evolution of part design, shops frequently find themselves called upon to thread holes with a wider range of diameters, depths and thread pitches. Consecutive production of a high quantity of identical holes has become a much rarer phenomenon. Tools with the flexibility to thread a broad variety of holes provide the agility many shops need to stay competitive.
These factors, combined with breakthroughs in machine capabilities and tool design, have led many companies to adopt thread milling as a preferred process. Whether a shop is considering shifting to this process or has already made the transition, recent advancements in thread mills merit serious attention and consideration.
Thread Mills: The Tools
There are three basic categories of thread mills available today.
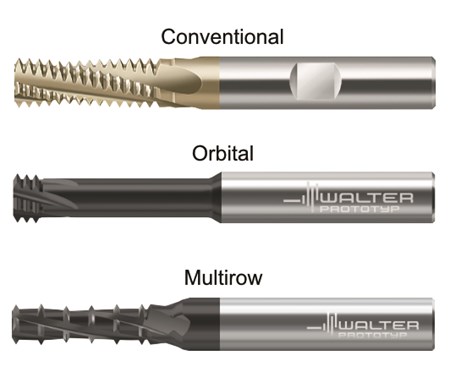
Basic types of thread mills.
Conventional thread mills feature closely spaced teeth along the length of their cutting body.
Orbital thread mills feature a either a single tooth or tightly spaced grouping of two or three teeth located at the far end of the cutting body.
Multirow thread mills, a new class of tool developed and introduced by Walter, split the difference between these two approaches. They feature multiple teeth that are located relatively far apart, with as much as a 1-inch space between one set of teeth and the next.
Each of these types of tools can be found in both solid carbide and indexable insert versions.
Thread Milling: The Processes
All three categories of thread mills can be applied in two basic ways. Conventionally, thread mills are fed downward into a hole, similarly to a thread tap, except only engaged with a portion of the circumference of the hole. This approach works well with hard materials yet can create chatter and present problems with surface finish.
Alternatively, climb milling, also commonly referred to as synchronous milling, can be applied. In this process, the tool starts at the bottom of the hole and works outward towards the hole’s surface. This eliminates the problem with chatter but creates a new issue. The tool being engaged with the workpiece to the hole’s full depth creates much more deflection. As a result, the process often results in conical threads, where the threads are tighter at the bottom of the hole than the top.
To avoid conical threads, many shops using climb milling incorporate a spring pass into their application. Essentially, this is coming back for a second pass, removing a very small amount of material to even out the threads. Unfortunately, while very little material is removed, the process generates an amount of heat and wear similar to the initial pass, effectively reducing tool life by as much as half. Some shops attempt to mitigate this loss by taking a 70/30 approach, where 70% of the material is removed on the first pass and 30% is removed on the second. This allows for the use of more aggressive cutting data to bring down cycle times.
Selecting the right process, as well as the right tool, has a dramatic impact on the success of a manufacturer’s thread milling processes, so it is important to make an informed decision that considers multiple aspects of the specific application.
Optimization: Choosing the Right Tools and Processes
As previously mentioned, thread mills in general will provide the most value when dealing with more challenging materials and a variety of hole dimensions. Manufacturers who are threading extremely high quantities of identical holes in highly machinable metals may be best served by sticking with thread tapping. But for high-cost components in difficult-to-machine materials, the increase in process security alone makes a very compelling case for moving to thread mills.
When choosing the best thread mill for a specific application, three key factors should steer the decision: batch size, depth, and diameter. Obviously, for prototyping or very small production runs, productivity will have a smaller impact on the overall profitability of the job. In those instances, a conventional thread mill is likely the most cost-effective solution.
For higher quantities of holes, depth comes into play. Shallow holes may be best served by an orbital thread mill, as there will be both low engagement and low deflection. With deeper holes, a multirow tool will provide superior performance to an orbital tool, and its advantages over a conventional tool become very apparent at higher quantities.

Walter multirow thread mill
Due to their high levels of engagement with the workpiece, conventional thread mills are significantly limited in the speeds and feeds at which they can be run. In turn, running with lower cutting data increases wear on the tool, resulting in the need for monitoring and adjustment to avoid producing undersized threads or risking tool breakage.
With the multirow approach, much less of the tool is actively engaged with the part at any given time. This allows for much more aggressive cutting data, which produces less wear and can be run with much more predictable performance.
The chart below illustrates this fact. It reflects actual results from a cutting test for three distinct options: 1) climb milling with a multirow tool with the 70/30 approach; 2) climb milling with a multirow tool with a spring pass and 3) conventional threading with a multirow tool.
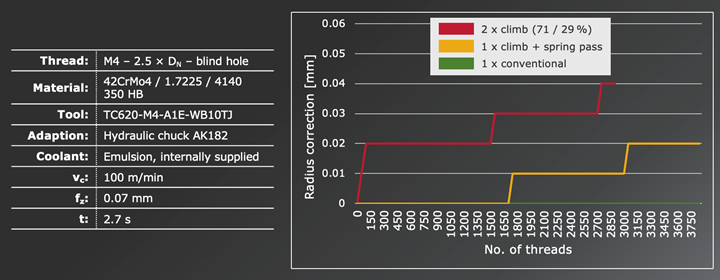
The use of a multirow thread mill significantly increases tool life and reduces the need for manual adjustments.
With the 70/30 climb milling approach, the tool produced approximately 3,000 holes, however the red line shows required adjustments at the ~150, ~1,500 and ~2,800 thresholds. The same tool using a light spring pass, represented by the yellow line, was able to thread the full lot’s 3,800 holes, with adjustments needed at the ~1,700 and ~3,000 marks. When using the multirow tool with a conventional strategy, all 3,800 holes were produced without requiring a single adjustment for tool wear, as seen by the green line across the bottom of the graph.
In practical terms, this demonstrates how the use of a multirow thread mill, combined with the best strategy for the material and depth of cut, minimizes the manual intervention required by a threading process. This both reduces the strain on a company’s labor pool and enables confident lights-out production.
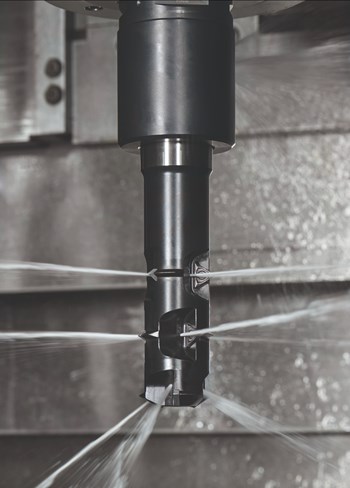
For hole diameters greater than 1 inch indexable tools can provide a more cost effective option.
Finally, whether threading deep or shallow holes, diameter will directly impact whether a solid carbide or indexable tool should be selected. For diameters less than 1 inch, a solid carbide option will typically provide the best combination of return and results. For diameters larger than that, indexable tools will reduce costs, as it becomes more cost effective to use inserts to replace the cutting portion of the tool rather than the entire body.
The impact of hole diameter holds true for all types of thread mills, but switching to an indexable multirow tool provides an additional layer of benefit. First, the use of smaller, triangular inserts, each with three cutting edges, helps to minimize cost. Beyond that, the tools’ design allows them to quickly and efficiently be switched to different thread pitches. Walter multirow indexable tools also feature 1-inch spacing between inserts, making it simple and intuitive to change the threads per inch. This extra level of flexibility reduces inventory costs and simplifies operations.
It is also worth noting that material type has little bearing on the type of thread mill selected. For each type, a wide range of modern substrates and coatings are available, allowing them to be effectively applied across a broad spectrum of materials.
An Expert Partner is Priceless
Shifting to thread mills yields significant benefits for many manufacturers, but choosing the right tool requires examination of a shop’s applications and operations. Walter has long been a tooling expert and is constantly pushing the evolution of thread mills. The company introduced the multirow concept several years ago and has also just recently introduced DeVibe technology that uses an anti-vibration land to produce nearly chatter-free threads in most applications. This DeVibe technology is available in both multirow thread mill varieties, solid carbide and indexable.
Walter’s experts are always available to discuss your applications and assist with cost and productivity studies. Whether you work with Walter or any other company, partnering with a premium and reputable cutting tool provider will grant you access to expertise in materials and processes, enabling you to identify an optimum solution with a sustainable competitive advantage.
Please visit the website for more information on Walter Thread Milling Cutters.