Toolholders
The Toolholder is the essential connection between the machining center and the cutting tool. The toolholder fits into and is secured by the machining center’s spindle, and in turn, secures the cutting tool such as a drill or end mill by clamping onto its shank. The taper of the toolholder matches the toolholder interface of the particular spindle. Toolholder tapers are often conical, including CAT and BT taper specifications. A different kind of taper, HSK, is not tapered at all, but instead includes a variety of flanges for securely locking the toolholder in place. Toolholders use different mechanisms for clamping the tool including set screw, collet, hydraulic compression and shrink-fit.
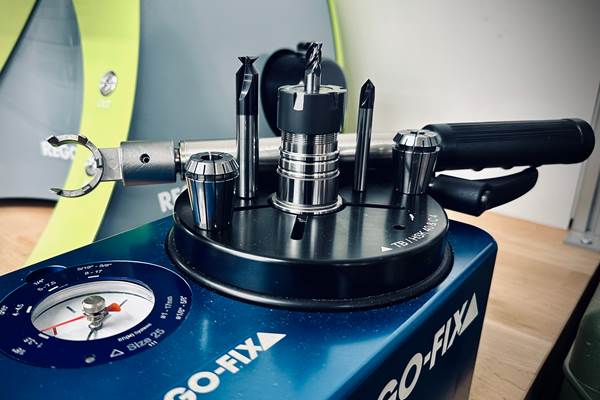
ESSENTIAL READING
VIEW ALLHow to Manage Cutting Tool Inventory in a Small Job Shop — The One-Person Shop #4
Working in short lead times means maintaining a large range of tools to be ready. What is the right way to stock and organize this investment?
WatchCutting Tool Technology Aids Lights-Out Machining Applications
These features can help improve cutting tool stability, standardize cutting performance and extend tool life, enabling shops to confidently run unattended shifts.
Read MoreWhat To Consider When Adding Angle Heads
Angle heads can enable a three-axis machine tool to be more versatile. That said, this shop explains that there’s more to getting started using them than simply loading them into a machine’s spindle.
Read MoreVideo Shows How to Check Toolholder Runout
Here’s a video that explains how to check the runout on a collet chuck toolholder.
Read MoreA Machinist’s Guide to Toolholder Maintenance
Techniks’ “Machinist’s Guide to Toolholder Maintenance” can be a handy reference for inexperienced machinists and shop veterans alike.
Read MoreWhy the Y?
See how Y-axis toolholders enable Swiss-type lathes to realize better chip control.
Read MoreLatest Toolholders News And Updates
Tungaloy Grooving Toolholders Provide Highly Stable Machining
TungHeavyGroove includes an enhanced insert clamping design for maximum tool rigidity.
Read MoreSeco Tooling Lineup Promotes Optimized Part Processing
The company’s expanded tooling lineup is aimed at applications ranging from general ISO turning to high-volume hard turning and deep-hole drilling.
Read MoreMarubeni Citizen-Cincom ATC Enables Flexible Machining
Westec 2023: The ATC tooling provides an environment where the tool setting for machining several types of workpieces can be completed in a single setup.
Read MoreFive Common Mistakes Shops Make with ER Collets (And How to Prevent Them)
Collets play a crucial role in the machining process, so proper tool assembly and maintenance is important. Here are five potential pitfalls to avoid when using ER collets.
WatchHaimer Shrink-Fit Machine Features Integrated Cooling
Westec 2023: Power Clamp Air i4.0 Eco provides smooth and clean cooling of all kinds of toolholders or collets by air, without dirt and water residue.
Read MoreRego-Fix Toolholding System Reduces Coolant Consumption
MQL PG collets are designed for machines using one-channel, internal through-spindle MQL systems.
Read MoreFeatured Posts
How to Troubleshoot Issues With Tool Life
Diagnosing when a tool is failing is important because it sets an expectation and a benchmark for improvements. Finding out why gives us a clue for how to fix it.
Read MoreSimulation and Tooling Secure High-Value Work
Simulation software and careful attention to tooling parameters have enabled Major Tool to take on ambitious projects with its complex machinery.
Read MoreIMTS Takeaways From the Modern Machine Shop Editorial Team
The first in-person IMTS in four years left the MMS editorial staff with a lot to digest. Here are a few of our takeaways from the show floor.
WatchFixturing for the Automated Age
Koma Precision’s booth at IMTS 2022 features practical demonstrations of rotary tables, right angle heads and more.
Read MoreHaimer USA Models a Streamlined Toolroom
Haimer USA is celebrating its 20th anniversary with a live demonstration of its digital toolroom. Find out more past the aluminum panther.
Read MoreAll-Around Mill Improves Productivity and Cost for Valve Job
Adopting a mill with a double-negative rake and pockets compatible with multiple insert geometries enabled Progressive Metal Service to increase feed and lower scrap rates for a valve.
Read MoreFAQ: Toolholders
What is a HSK toolholder?
HSK, meanwhile, works by elastically deforming the toolholder. Fingers inside the hollow shank of the toolholder clamp the holder by pushing out. High spindle speed helps this interface, because the centrifugal force strengthens this clamping.
Source: Testing Measures Impact of Toolholder Interface Rigidity
How does a hydraulic toolholder work?
The hydraulic toolholder works by using fluid to compress an internal membrane within the holder body. The hydraulic fluid delivers uniform pressure around the membrane allowing it to compress equally around the periphery of the cutting tool. Basically, that’s how the hydraulic toolholder delivers its high concentricity specs.
Source: Why Use Hydraulic Toolholders
What is a toolholder?
The toolholder is the connection between the machining center and the cutting tool, employing clamping mechanisms such as set screws, collets, and shrink-fit.