Turning Machines
“Turning” defines the work that is traditionally done on a lathe. “Turning centers” is a term sometimes applied to machines with secondary spindles and/or rotating tools for milling and drilling. Another term, “turn/mill or multitasking” describes machines that can be thought of as being just as capable at milling and drilling as they are at turning. Lathes, turning centers and turn-mill machines can have horizontal or vertical spindles, with horizontal being most common. Machines with a vertical spindle are generally called a vertical turret lathe, or VTL. If the workpiece is held from above by the vertical spindle, then this type of turning machine is generally called an inverted vertical lathe.
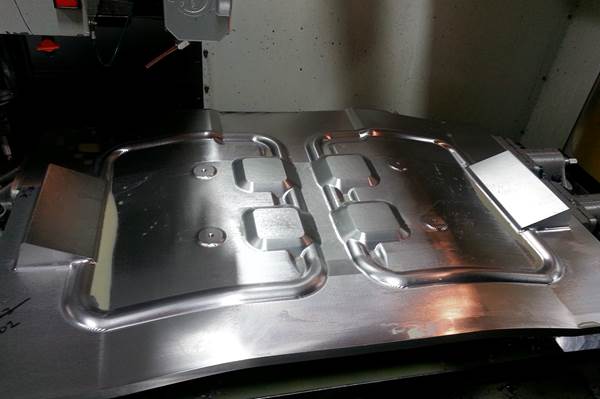
ESSENTIAL READING
VIEW ALL4 Tips for Staying Profitable in the Face of Change
After more than 40 years in business, this shop has learned how to adapt to stay profitable.
Read MoreHow to Start a Swiss Machining Department From Scratch
When Shamrock Precision needed to cut production time of its bread-and-butter parts in half, it turned to a new type of machine tool and a new CAM system. Here’s how the company succeeded, despite the newness of it all.
Read MoreBuying a Lathe: The Basics
Lathes represent some of the oldest machining technology, but it’s still helpful to remember the basics when considering the purchase of a new turning machine.
Read MoreThreading On A Lathe
The right choices in tooling and technique can optimize the thread turning process.
Read MoreChoosing Your Carbide Grade: A Guide
Without an international standard for designating carbide grades or application ranges, users must rely on relative judgments and background knowledge for success.
Read MoreMachining 101: What is Turning?
Turning uses a lathe to remove material from the outside of a rotating workpiece, while boring does the same from the inside of a rotating workpiece.
Read MoreLatest Turning Machines News And Updates
Inside the Premium Machine Shop Making Fasteners
AMPG can’t help but take risks — its management doesn’t know how to run machines. But these risks have enabled it to become a runaway success in its market.
Read MoreFryer Lathe Features Multiple Operation Modes
Easy Turn Toolroom Turning Lathes enable operators to use manual, semi-CNC or full-CNC modes.
Read MoreInverting Turning and Five-Axis Milling at Famar
Automation is only the tip of the iceberg for Famar, which also provides multitasking options for its vertical lathes and horizontal five-axis machine tools.
Read MoreTsugami America Lathe Enables Simultaneous Machining
The BW129Z Swiss-type lathe uses a three-path control system and dual independent-gang slides to reduce cycle time and produce complex parts quickly.
Read MoreOkuma Demonstrates Different Perspectives on Automation
Several machine tools featured at Okuma’s 2023 Technology Showcase included different forms automation, from robots to gantry loaders to pallet changers.
Read MoreMazak Offers Horizontal Turning Center for Flexible Machining
The QT-Ez Series comes equiped with optional spindles, chuck sizes and tailstocks.
Read MoreFeatured Posts
Swiss-Type, Live Tooling Lathes Help Turn Company Around
New leadership’s investment in Swiss-type and live tooling lathes has enabled Rathburn Tool & Manufacturing to expand into new markets, reversing the company’s sluggish growth.
Read MoreHow to Start a Swiss Machining Department From Scratch
When Shamrock Precision needed to cut production time of its bread-and-butter parts in half, it turned to a new type of machine tool and a new CAM system. Here’s how the company succeeded, despite the newness of it all.
Read MoreDigital Demo: People and History Drive Solutions
Bourn & Koch has long provided unique manufacturing solutions. However, the people who work at Bourn & Koch enable the company to deliver value to each partner they work with. From service to assembly to engineering, each step builds on the solution—helping you solve your most challenging manufacturing problems. (Sponsored)
WatchSMEC America Showcasing Machines' Reliability and Rigidity
SMEC America is running demonstrations on its machines both old and new at its IMTS booth, with engineers on hand to help answer questions.
Read MoreExpand Machinery Swiss-Type Machine Offers 33 Tool Positions
Expand Machinery’s Genturn-52CS Y2 features a subspindle as well as dual C and Y axes to enable multiple operations in a single handling.
Read MoreInside an Amish-Owned Family Machine Shop
Modern Machine Shop took an exclusive behind-the-scenes tour of an Amish-owned machine shop, where advanced machining technologies work alongside old-world traditions.
Read MoreFAQ: Turning Machines
What is turning?
Turning is the process of using lathes to remove material from the outer diameter of a rotating workpiece. Single-point tools shear metal from the workpiece in (ideally) short, distinct, easily recyclable chips.
Source: Machining 101: What is Turning?
What is a lathe?
One of the key characteristics of a lathe, unlike a vertical or horizontal milling machine, is that the workpiece turns, as opposed to the tool. Thus, lathe work is often called turning. Turning, then, is a machining process used to make round, cylindrical parts.
Source: Buying a Lathe: The Basics
What is the basic configuration of a lathe?
The basic two-axis lathe consists of a headstock with spindle, chuck for holding the part, lathe bed, carriage and cross-slide, tool turret and tailstock. While most lathes have a moveable tailstock to support the workpiece at the end, away from the chuck, not all machines come with this feature as a standard. A tailstock is particularly useful, however, when the workpiece is relatively long and slender.
Source: Buying a Lathe: The Basics
What kinds of spindles do lathes typically have?
The spindle on a turning center is either belt-driven or direct-drive. Generally, belt-driven spindles represent older technology. They speed up and slow down at a lower rate than direct-drive spindles, which means cycle times can be longer. If you’re turning small-diameter parts, the time it takes to ramp the spindle from 0 to 6,000 rpm is significant. In fact, it might take twice as long to reach this speed than with a direct-drive spindle.
What are the types of programmable tailstocks?
A built-in, numerically controlled tailstock can be a valuable feature for automated processes. A fully programmable tailstock provides more rigidity and thermal stability. However, the tailstock casting adds weight to the machine.
There are two basic types of programmable tailstocks—servo-driven and hydraulic. Servo-driven tailstocks are convenient, but the weight they can hold may be limited. Typically, a hydraulic tailstock has a retractable quill with a 6-inch stroke. The quill also can be extended to support a heavy workpiece, and do so with more force than a servo-driven tailstock can apply.
What are some variations of the basic lathe configuration?
Slant-bed lathes provide a number of advantages, while multitasking lathe configurations might open up possibilities heretofore unthought of.
The slant-bed lathe design is probably the most common and well-known configuration in today’s CNC lathes. Typically, the bed of the lathe slants at a 30- or 45-degree angle, although some 60-degree models also are available.
Multitasking machines are often built on a turning center platform. These machines use rotary tools to combine several cutting processes such as turning, milling, drilling, tapping, grooving, threading and deep-hole boring on one machine.
Source: Buying a Lathe: Slant-Beds and Multitasking Configurations