
Electric vehicle batteries depend on coatings to help with thermal management, electrical shielding and more. All images courtesy of PPG.
If you’ve followed the emergence of electric vehicles (EVs) onto the automotive market, you’ve heard a lot of discussion around lightweighting: the practice of building lighter vehicles to help with fuel efficiency. But developments around EV batteries have the biggest potential right now for improving EV performance, bringing down cost and encouraging adoption.
According to Anthony Schiavo, senior analyst at Lux Research, EVs will require less lightweighting — not more. “Light weighting can be cost-effective against batteries at today’s prices, but our expectations are that battery pack sizes will go up. Lightweighting is more effective as the battery pack size goes up. The reality is that know there’s a much bigger opportunity for cost reduction from the battery side.”
Battery packs require custom solutions

Each OEM has its own battery pack design, with a unique set of needs and challenges.
Tomorrow’s batteries will need to cost less and go further while maintaining high safety standards. As OEMs tweak their battery designs, coatings play an essential role. To understand how coatings can improve efficiency, it helps to understand what EV batteries consist of. Most EVs run on battery packs — a number of lithium-ion battery cells grouped together.
That’s where the consensus on batteries ends, according to David Malobicky, general manager of mobility at PPG (Pittsburgh, Penn.). “Every OEM has their specific design for their batteries and their battery pack,” Malobicky explains. “It’s considered their custom solution.”
Each battery pack design has its own set of needs and challenges that need to be addressed, which is why flexibility and diversity of offerings is essential for coatings providers in the EV space. Regardless of the architecture of the individual pack, they all need fire protection, corrosion and impact protection, temperature management and electrical shielding. Coatings can meet those needs.
The role of coatings
One essential role for coatings is temperature management. For batteries to be efficient, thermal management is key. Malobicky explains, “Batteries don’t operate efficiently at extremes, whether they’re too hot or too cold. They won’t last as long or perform as efficiently. Keeping batteries at an optimum temperature range is critical.” In order to maintain batteries at the best functional temperatures, OEMs employ battery thermal management systems (BTMS), which are supported by coatings.
Common BTMS strategies include applying “gap filler” or thermal conductivity coatings between battery plates and modules or between cooling coils and plates. PPG’s solutions are liquid, so they can be applied robotically or manually.
From a consumer safety standpoint, coatings that protect against fire and dielectric currents are among the most essential. Lithium-ion battery cells are full of flammable solvents, so intumescent coatings help protect batteries from fire damage and mitigate the risks of fires breaking out in the first place.
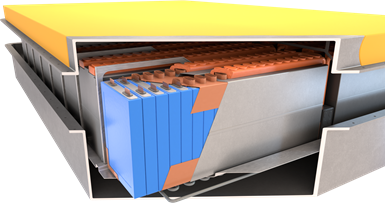
Battery packs require protection from electromagnetic interference.
Battery packs also require protection from electrical interference. “There’s a lot of metal components in a battery pack,” Malobicky explains. “If you get to metal components close to together enough, and there’s electricity going through one of them, you can get an arcing event.” Previously, dielectric coatings were mostly films or tapes, but coatings have evolved to eliminate gaps, bubbles and seam failures in their place. Applying these coatings can be automated, making this a more attractive option than more manual processes like taping. PPG’s solutions can be applied to battery cells, metal housing, pack shells, cooling system components and bus bars and connecters, and they have high and low temperature process options.
The thing is, there’s no one size fits all product. Each of these features is currently provided by a different coating, which adds another layer of complexity. Engineers at PPG are working to combine functionality, so one coating can provide multiple features. Until that is perfected, coating EV batteries requires a lot of customization.
Malobicky and his team work with OEMs to determine the right coatings with the right applications for a given battery pack. “We work very intimately with the engineers that are designing the battery packs so we can understand their problems, their issues, their requirements. Then, we offer a customized solution, not only from a material standpoint, but from an application standpoint as well. We work with the OEMs to get the material qualified, but also with their tiered suppliers so that they can adopt the application solution that that best fits,” Malobicky explains.
The future of EVs
“Right now, the global production for electric vehicles is around two million. The projections are around 10 million or more by 2025, and then 40 million plus by 2030,” Malobicky says. Coating materials and technology will have to keep up with that growth, with scalability being a key concern. PPG has its eye on automation: its offerings can be applied through high-volume automated processes. “In some of these areas, using a coating in general is an innovation. Using coating in place of another, more manual process brings efficiency advantages,” according to Malobicky. Protective coatings are also important, and PPG offers corrosion and impact protection via electrocoating, powder coating and liquid coating.
PPG offers services ranging from designing a coating line, to operating a coating line within an OEM plant, to coating parts in its own facility. The ultimate goal is to lower the cost for OEMs to manufacture electric vehicles, which will lower the consumer price and bring the cost of EVs more in line with internal combustion engines.
Malobicky sees opportunities for coaters growing as EV demand increases. “Even with the pandemic, the projections are that there will still be growth in EV builds year on year from 2019 to 2020. There aren’t a lot of industries that can say that they grew, given the pandemic. And if you look at the overall automotive growth rate, it’s flat. The number of cars being sold is not likely to grow. So, if you’re a company that has content on vehicles, you’re not going to grow by just market growth. You have to grow by content per vehicle. What better segment of the automotive market to get content on than EVs?”
Related Content
Arch Cutting Tools Acquires Custom Carbide Cutter Inc.
The acquisition adds Custom Carbide Cutter’s experience with specialty carbide micro tools and high-performance burrs to Arch Cutting Tool’s portfolio.
Read MoreSandvik Coromant on Acquisitions: Solutions Entail More Than the Tool
A Q&A with global president Helen Blomqvist explores the cutting tool maker’s acquisition of CAM software companies and how this connects to, among other things, electric vehicles.
Read More4 Tips for Staying Profitable in the Face of Change
After more than 40 years in business, this shop has learned how to adapt to stay profitable.
Read MoreMarposs Celebrates its Past, Eyes Future Opportunities
During its open house in Auburn Hills, Michigan, Marposs presentations focused on future opportunities across growing industries such as EV and semiconductors.
Read MoreRead Next
Evolving Automation in Automotive
A look at the latest liquid coating technologies for the automotive sector from leading robotics and surface finishing technology providers
Read MoreThe Cut Scene: The Finer Details of Large-Format Machining
Small details and features can have an outsized impact on large parts, such as Barbco’s collapsible utility drill head.
Read More3 Mistakes That Cause CNC Programs to Fail
Despite enhancements to manufacturing technology, there are still issues today that can cause programs to fail. These failures can cause lost time, scrapped parts, damaged machines and even injured operators.
Read More