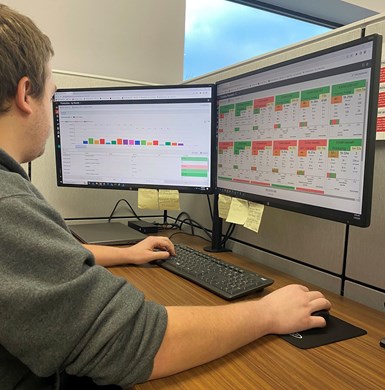
Jonathan Langdon, quality engineer at Enjet Aero, observes a Vimana dashboard, where users can see metrics like machine utilization, downtime and more.
Photo Credit: Enjet Aero
Enjet Aero, a manufacturer of jet engine precision-machined and fabricated components and assemblies with nine facilities and a wide array of capabilities, relied on employees to record data from shop floor processes in spreadsheets, a time-consuming and labor-intensive task. Metrics were estimates, making it difficult to understand actual performance, and the lack of hard, real-time data restricted the company’s ability to investigate downtime causes and cycle time variance.
This challenge drove Enjet to invest in Vimana’s Industrial Analytics software to make day-to-day process improvements, reduce costs and increase capacity.
After a successful trial at Enjet’s facility in Terre Haute, Indiana, the company’s machine utilization at the location rose from 378 hours per machine in April 2021 to 519 hours per machine in July 2022. By reducing both unplanned and planned downtime, capacity and availability increased by 35%, while production hours rose to 500 hours per machine.
“It’s kind of a shock to everyone — when it gets installed — how little the equipment is actually utilized,” says Perry Pecaut, Enjet’s vice president of manufacturing.
These gains enabled Enjet to invest more in its equipment and its people. The company invested $30 million in new equipment over the last two years, and operators have received salary increases after they surpassed performance targets. Enjet’s goal is to achieve 17.2 production hours per day 350 days per year — around 6,000 hours per year — on certain types of machines.
With data from Vimana providing a bird’s eye view of utilization metrics, Enjet was able to automate a process that extracts the data into a daily report showing which machines are meeting or missing utilization goals. These reports, which also include a week of data history, help the Enjet team focus their attention on where improvements are most necessary and how to make them.
Fixing the Fixturing
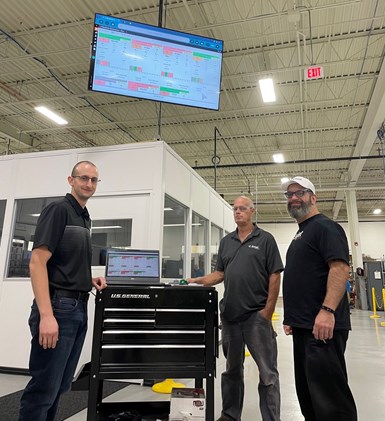
With Vimana providing a macro-scale view of data regarding machine utilization and uptime, Enjet Aero has increased its production hours and machine utilization, leading to investments in its personnel and new equipment.
Photo Credit: Enjet Aero
After deploying Vimana and referencing its data for areas of improvement, the engineering team quickly understood how much faster they needed to change part number to part number. These realizations drove Enjet to use more modular fixturing.
Modular fixturing can be reassembled between jobs to secure a workpiece with a different shape. The versatile setup of modular fixturing can lead to long-term cost savings and storage space. Modular fixturing can be designed and assembled more quickly than dedicated fixturing with the main frame always being in place on the equipment. In Enjet’s case, using the data from Vimana helped its team identify modular fixturing as a potential time-saving solution.
“You’ve got to be able to think outside the box. When you really start seeing how little you use the equipment, you’ve got to be willing to do something different, like developing enough fixturing to get through the shifts that are difficult to man by holding more parts,” Pecaut says. “In a lot of cases, (the data) just drives you to a different type of equipment.”
In this case, the data has led Enjet to different equipment, new ways of identifying areas of improvement and a better idea of the overall progress toward reaching its production and utilization goals. Enjet uses alerts and notifies appropriate teams if machines are operating at lower speeds, unknown downtime exceeds 30 minutes or if machines have not produced for more than two hours.
Vimana helps prioritize these alerts by sorting based on reason code, the number of alerts and the most significant downtime duration.
With these features, Enjet quickly realized its newfound potential by increasing its utilization.
“It’s an evolution getting there. When we first implemented it in Terre Haute, they were working as hard as they possibly could and constantly saying, ‘There’s absolutely no way we will reach 500 hours per month,’” Pecaut says. “Today, they’re not having to work as hard and are hitting the goals.”
Related Content
Wireless Couplers Work Wonders for Workholding
Possibilities range from individual control of chuck jaws and tombstone fixtures to more reliable robots.
Read MoreShop Quotes Smarter, Works Harder with Machine Monitoring
Temco first installed MT-LINKi to optimize quoting. Now, the software helps the shop optimize its machines — and machine purchases.
Read MoreCan Connecting ERP to Machine Tool Monitoring Address the Workforce Challenge?
It can if RFID tags are added. Here is how this startup sees a local Internet of Things aiding CNC machine shops.
Read More5 Stages of a Closed-Loop CNC Machining Cell
Controlling variability in a closed-loop manufacturing process requires inspection data collected before, during and immediately after machining — and a means to act on that data in real time. Here’s one system that accomplishes this.
Read MoreRead Next
Machine Monitoring Is the First Step to Data-Driven Manufacturing and Industry 4.0
Before automating or digitalizing production, a company should streamline existing processes by setting up a machine-monitoring system.
Read More3 Perspectives on Machine Monitoring
A panel discussion at the recent Top Shops Conference focused on various points of view regarding the value of connecting machine tools to a network for monitoring performance and recording results. Because machine monitoring helps a shop make better decisions about manufacturing processes, it is a good example of data-driven manufacturing in action.
Read MoreFive Tips for Effective Machine Monitoring
A machine shop’s successful entry into machine monitoring reveals important points about what to do and what to expect.
Read More