HyWaSand demonstrates large-series production potential for automotive TP sandwich components
Storage compartment flap for truck interior produced via fully automated continuous fiber thermoplastic sandwich molding technology shows suitability for series manufacture.
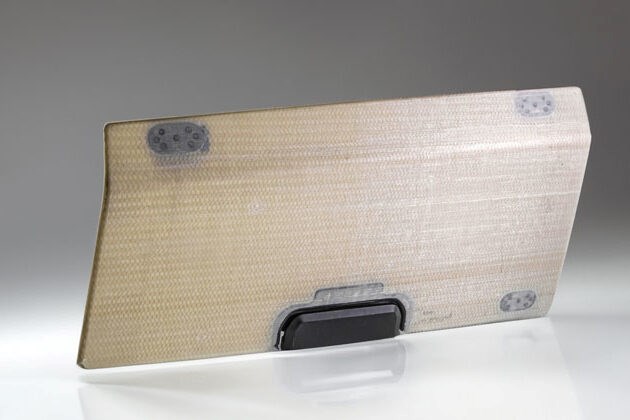
Demonstrator flap, which was created by thermoforming and functionalizing thermoplastic sandwich structures. Source | Fraunhofer IMWS
Under the HyWaSand project, Germany-based Daimler Truck AG (Stuttgart), ElringKlinger AG (Stuttgart), ThermHex Waben GmbH (Halle), Edevis GmbH (Leinfelden-Echterdingen), the Fraunhofer Institute for Microstructure of Materials and Systems (IMWS, Halle) and Austria-based Engel Austria GmbH (Schwertberg) have produced a storage compartment flap for a truck interior. The flap, made from thermoplastic composite sandwich semi-finished products, demonstrates the potential for saving weight with a thermoplastic sandwich molding technology and its suitability both for molded components and for use in large-scale production.
The project found that the use of composite materials — and a sandwich structure in particular, which consists of highly rigid and strong cover layers and a lightweight core — offers many advantages to commercial vehicle applications. In addition to high material efficiency, sandwich composites enable high weight-specific bending and buckling stiffness, suitable for heavy-duty structural components. It also enables potential weight savings of up to 70% compared to monolithic structures, with a load-bearing capacity that corresponds to or even exceeds that of metallic components.
One challenge to date, however, has been their manufacture via large-scale production processes. Partners in HyWaSand therefore looked at the use of thermoplastic composite sandwich semi-finished products, which can be produced efficiently in continuous processes and turned into components via automated manufacturing processes.
“The potential is huge. By manufacturing the components in large series, cost-efficient lightweight structures for interior and body components can be produced.”
A flap for a storage compartment in a truck cabin was produced as a demonstrator using this method. Key to its success was the thermoplastic sandwich molding technology developed at Fraunhofer IMWS. Based on a new type of thermoforming process, it was developed specifically for the fully automated production of continuous fiber-reinforced sandwich components with a thermoplastic matrix in large series. Thermoplastic sandwich semi-finished products, consisting of a thermoplastic honeycomb core and cover layers of fiber-reinforced thermoplastic unidirectional (UD) tape laminates, are heated in an infrared oven and, after automated transfer to the molding tool, 3D thermoformed and functionalized by means of injection molding.
“The TS molding technology proved to be very efficient in our project. We were able to show that it enables the efficient production of 3D molded and functionalized lightweight components in sandwich construction in the injection molding cycle, i.e., with cycle times of around one minute,” says Dr. Ralf Schlimper, who led the project at the Fraunhofer IMWS. “This shows the potential for further fields of application, such as the car body sector.”
When it comes to commercial vehicles, every gram counts. Thermoplastic sandwich molding technology offers great potential for lightweight construction. Source | Daimler Truck AG
For the project, partner ThermHex Waben GmbH focused primarily on the development of hybrid sandwich semi-finished products with a small cell width and functional polymer and metal foils to improve surface quality. In addition, the new development of continuously manufactured semi-finished sandwich products with even lower material use was driven forward.
In conjunction with necessary adaptation of the manufacturing process to make it suitable for series production, it was made possible to achieve a further reduction in cost and weight compared to the previous standard configurations and non-recyclable material alternatives from reaction injection molding (RIM) processes. At the semi-finished product level, 30-45% of the weight can be saved with the same material thickness or up to 22% of the weight with comparable mechanical performance and greater material thickness. This improved resource efficiency in materials use also has a proportionally positive effect on material costs and CO2 emissions.
In test structures, the project was able to demonstrate that components with Class A surfaces, which are particularly important for the automotive industry, can also be manufactured from thermoplastic semi-finished products in sandwich construction. Progress was also made for metal-plastic hybrid sandwich materials, such as the lamination of test structures with metallic cover layers using the TS molding process.
“There are still research questions that we want to continue working on,” says Schlimper. “This makes it all the more valuable that we have made great progress in the project in providing virtual engineering methods for process and component development and have also developed feasible test tools for various common component design features. The new possibilities for inline inspection and for suitable nondestructive testing methods to ensure component quality also enable us to rapidly bring the technology even closer to application in various cost- and weight-sensitive areas.”
According to Matthias Biegerl, who led the project at ElringKlinger, the consortium is “currently investigating the transferability of the results to customer development projects in order to facilitate entry into new market segments. The potential is huge. By manufacturing the components in large series, cost-efficient lightweight structures for interior and body components can be produced.”
Related Content
DN Solutions Responds to Labor Shortages, Reshoring, the Automotive Industry and More
At its first in-person DIMF since 2019, DN Solutions showcased a range of new technologies, from automation to machine tools to software. President WJ Kim explains how these products are responses to changes within the company and the manufacturing industry as a whole.
Read MoreElectric Vehicles Spark Bright Ideas
Ford alone expects to have production capacity for 600,000 electric vehicles by late 2023, and more than 2 million by the end of 2026. The effects on manufacturing are BIG.
Read MoreEliminating Automotive Defects Per Million With Automated Visual Inspection
This automotive manufacturer virtually eliminated PPM defect complaints after implementing an automated visual inspection system at its facility.
Read MoreSiemens and Mahle Partner to Develop Wireless EV Charging
Mahle will contribute its experience as an automotive supplier and Siemens will use its expertise in the field of charging infrastructure to develop wireless charging stations for electric vehicles.
Read MoreRead Next
Optiplan automotive sandwich panels optimized via AOC rPET resin series
Incorporation of AOC’s Synolite rPET resins into FRP cover sheets enables the development of more eco-friendly truck construction.
Read MoreFraunhofer IWS completes MFFD longitudinal fuselage joint using CONTIjoin technology
Thermoplastic composite upper and lower half shells for the Multifunctional Fuselage Demonstrator were welded using CO2 laser over a total length of 8 meters.
Read MoreDamage tolerance testing of sandwich composites: The sandwich CAI test
A new ASTM-standardized test method established in 2022 assesses the compression-loaded damage tolerance of sandwich composites.
Read More