April 2008 Issue
April 2008
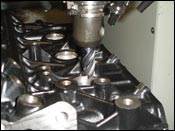
Features
Featured articles from the April 2008 issue of Modern Machine Shop
Factories Around The World Consume More Equipment
China’s growth dominates the world: machine tool output & consumption survey
Read More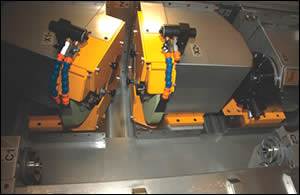
Hard Turning And Cylindrical Grinding Were Made For Each Other
Combining different machining processes on the same platform has been a major theme in machine tool design for two decades or so. The Studer S242 combines cylindrical grinding and hard turning. A look at this machine shows that both of these machining processes benefit when they share the same platform.
Read More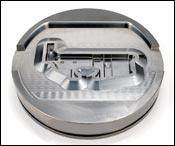
Hard Milling By The Numbers
Here are some speeds, feed rates and depths of cut for a productive hard milling process.
Read More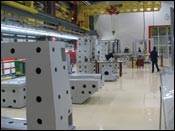
Dixi Rising
Heavy investment in this Swiss builder’s production facility will allow its output to rise just as the demand for large machine tools capable of nano-precision is also rising.
Read More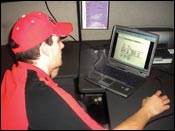
Molding Personnel
This mold shop has a full-time employee devoted to nothing but training.
Read More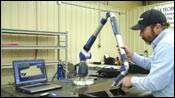
Increased Accuracy And Portability For Measuring Arms
Multi-axis, computer-aided measuring arms offer accuracy comparable to a CMM in a portable design. A new version of such an arm is said to be the first 8-foot measuring arm that can achieve an accuracy of 0.0007 inch.
Read More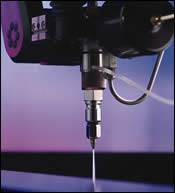
Zero Taper In Abrasive Waterjet Cutting
Abrasive waterjet machines use a high-velocity beam of water and abrasive particles to cut thick materials. This "floppy tool" has a tendency to cause tapered edges during cutting. Omax's IntelliMax software and Tilt-A-Jet technology is capable of producing zero taper without adversely affecting machining speeds. IntelliMax controls the cutting paths to ensure that the machine is operating at the highest possible speeds at all times. The Tilt-A-Jet can position the nozzle at the angle calculated by the software to offset the natural taper from the waterjet. The tapering effect is moved to the scrap side of the parent material, thus leaving square edges (zero taper) on the part.
Read More