Touch Probe Calibration: Does Your Standard Shape up?
These two shops’ experiences reveal the value of choosing artifacts that match the geometry of the measured feature as closely as possible.
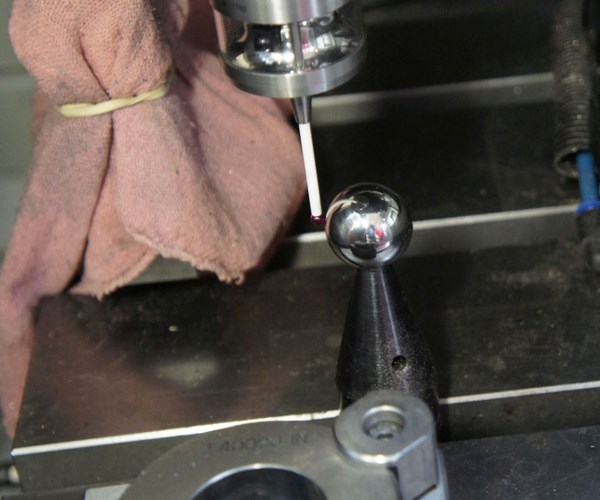
Spherical calibration standards, which are permanently mounted to machine tables at Dynamic Tool, are recommended for 3D measurement routines.
Although they do very different work for very different industries, Dynamic Tool & Design and Integral Machining LTD both emphasized a similar point about touch probe calibration during recent shop visits. That is, the more closely an artifact matches the geometry being measured, the greater the precision of the resulting inspection routine.
At Dynamic Tool, a 38-employee Milwaukee-area plastic injection mold manufacturer, this point came up as part of a broader discussion about a transition to conducting part measurements on machine tools (this June-issue feature article covers that journey). Although the company had long taken advantage of touch probing routines on its 13 workhorse hard milling and sinker EDM machines, the measurements were previously limited to indicating (that is, ‘zeroing-in’ workpieces). For these 2D routines, a ring-shaped standard of known dimension was more than sufficient to calibrate the probe. Since moving into 3D part measurements, however, the shop has installed spherical artifacts on its machine tables. Because the probe can contact the evenly round sphere from a far greater number of angles than the ring—angles that are more representative of how the probe will approach various features on the workpiece—the set of compensating offsets for tip diameter, deflection and so forth is more thorough.
The story at Integral Machining is similar. In this case, however, the 9-employee, Toronto-area precision machine shop opted for a ring over a sphere. The job in question came from one of the shop’s newer customers: microfluidics and photonics industry companies that often require meeting tolerances in single-digit microns, far more precise than anything the shop had seen prior to about 2010 (this July-issue feature article covers Integral’s journey into micron-tolerance machining).
In this particular case, such tight tolerances had been called out for a series of critical bore diameters that were proving difficult to measure repeatably on the shop’s CMM. The shop’s eventual solution was to supplement the datum sphere the shop had historically used to calibrate touchprobes with a 2.5-mm-diameter, cubic zirconia ring gauge with dimensions guaranteed to 6 decimal places. Granted, the sphere retains the advantage for 3D measurements. For this portion of this job, however, calibrating against the ring gauge enabled the shop to make even finer adjustments to account for the diameter of the probe tip—adjustments that proved critical to ensuring more accurate and repeatable measurements of the 2.5-mm-diameter bores.

Integral Machining’s cubic zirconia ring gauge proved better than the shop’s datum sphere for precise, 2D bore diameter measurements.
Granted, I’ve attempted only to take a basic, “30,000-foot view” of this topic here. Boiled down to essentials, though, it seems to me that calibrating against the 2.5-mm-diameter ring gage was a better option for Integral Machining because this routine precisely mimicked the actual measurements that would be conducted on the 2.5-mm-diameter bores. Indeed, production manager Andrew Sweeting says he might consider using cylindrical artifact to ensure precision on a particularly critical outside diameter.
All in all, both shops’ experiences demonstrate that taking another look at probe calibration artifacts might be more than worth it for any shop encountering difficulties with precision or repeatability on a particularly critical measurement.
Related Content
Ballbar Testing Benefits Low-Volume Manufacturing
Thanks to ballbar testing with a Renishaw QC20-W, the Autodesk Technology Centers now have more confidence in their machine tools.
Read More6 Machine Shop Essentials to Stay Competitive
If you want to streamline production and be competitive in the industry, you will need far more than a standard three-axis CNC mill or two-axis CNC lathe and a few measuring tools.
Read MoreHow to Calibrate Gages and Certify Calibration Programs
Tips for establishing and maintaining a regular gage calibration program.
Read MoreUnderstanding Errors In Hand-Held Measuring Instruments
Different instruments (and different operators) are prone to different errors.
Read MoreRead Next
3 Mistakes That Cause CNC Programs to Fail
Despite enhancements to manufacturing technology, there are still issues today that can cause programs to fail. These failures can cause lost time, scrapped parts, damaged machines and even injured operators.
Read MoreThe Cut Scene: The Finer Details of Large-Format Machining
Small details and features can have an outsized impact on large parts, such as Barbco’s collapsible utility drill head.
Read More