Another Giant Leap for AM — New Standards
Additive manufacturing standards help bring order and clarity to a burgeoning and chaotic field. Recently, many new ones have emerged.
Summary of Aerospace Materials Specification (AMS) Standards for AM approved and in development by SAE International. Photo Credit: John Barnes, The Barnes Global Advisors
With everything going on these past 18 or so months, it would be easy to have missed all the new standards that emerged — but then again, who waits with bated breath for new standards to be released? Certainly not most engineers or designers, but, in additive manufacturing (AM), new standards help bring a semblance of order and clarity to a burgeoning and chaotic field.
Why the flurry of AM standards? With everyone in lockdown and unable to travel, maybe the pandemic actually helped accelerate standards development. I mean, why wait for a face-to-face meeting when its possible to simply hop on Zoom anytime from anywhere and debate the wording on the latest standard in development? Or maybe all of the committee members were able to be present, discuss, revise and approve new standards much more rapidly with fewer distractions? Who knows exactly what happened and why, but the output has been a boon for AM. Now, the challenge is keeping up with them all.
While ASTM/ISO have published the most AM standards, SAE International wins the prize for most active Standards Development Organization (SDO) the past 18 months, in my opinion. Specifically, its Aerospace Materials Specification (AMS) AM Additive Manufacturing Metals Committee has issued 11 new standards since January 2020. While many of these are for powder feedstocks used in aerospace AM applications, the committee has also released standards for wire-fed directed energy deposition (DED) for laser (AMS 7010), electron beam (AMS 7027) and electron beam powder bed fusion (AMS 7007), as well as binder jetting (AMS 7022). Meanwhile, 19 additional standards are listed as works in progress, including a standard practice for designing AM components in an aircraft system (AMS 7042) — one that I am anxiously awaiting, given my design for AM (DFAM) interests. Wait, did I just write that I was anxiously awaiting a standard? I am such a geek.
In addition to these 30 — yes, 30! — issued and forthcoming standards for AM aerospace applications, NASA released its Additive Manufacturing Requirements for Spaceflight Systems (NASA-STD-6030) in April 2021. This standard creates NASA-wide requirements for AM and is accompanied by NASA-STD-6033, which specifies requirements for equipment and facility control for additive manufacturing. Of course, if NASA’s Jet Propulsion Laboratory (JPL) had waited for either of these new standards to be released, it would not have landed and operated AM parts on Mars back in February 2021. In fact, PIXL and MOXIE, two of the instruments on the Mars 2020 Perseverance Rover, were only made possible by AM, and I was lucky enough to see Perseverance undergoing final testing at JPL in January 2020 before it was launched. I still remember flying back home from that trip and wondering why so many people were wearing face masks in LAX.
Another document for AM qualification and certification is the Recommended Guidance for Certification of AM Component, which was issued by the Aerospace Industries Association (AIA) Additive Manufacturing Working Group in February 2020. It is freely available online and provides useful guidance on process control documentation, operator training and software configuration control, as well as supply chain qualification for AM. Its guidance on material property development for AM was particularly easy to digest, as was the corresponding discussion on part design and qualification.
Speaking of AM operator training, I recently learned that the European Federation for Welding, Joining and Cutting (EWF) leveraged its training, qualification and certification system for welding personnel to create three levels of certification for AM operators and four levels of certification for AM engineers. The graphics on EWF’s AM website are easy to navigate, and the accompanying information provides a good reference or starting point for any company new to AM.
ASTM remains very active as well, with AM standards efforts coordinated and supported by its Additive Manufacturing Center of Excellence. ASTM’s E07 Nondestructive Testing Committee released the Standard Guide for Nondestructive Examination of Metal Additively Manufactured Aerospace Parts After Build (ASTM E3166) in August 2020. This standard provides a wealth of information on a variety of nondestructive evaluation technologies, including radiographic and x-ray computed tomography, eddy current evaluation, penetrant testing, thermographic testing, process compensated resonance testing, ultrasonic testing and optical metrology.
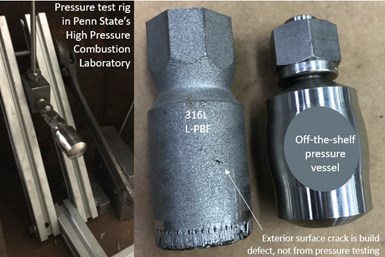
Pressure test rig (left) along with AM (middle) and off-the-shelf (right) pressure vessels in 316L stainless steel after testing; the AM pressure vessel did not deform (like the conventional one) nor burst under 2.5 times the rated load. Photo Credit: David Drewniak and Nick Nace, Penn State
Finally, the reason why I had pressure vessels on my mind last month: ASME issued its new standard, Criteria for Pressure Retaining Metallic Components Using Additive Manufacturing (PTB-13-2021) in May 2021. The standard outlines procedures for specifying and qualifying AM pressure vessels and includes details on testing procedures and witness sampling as well as chemical composition analysis, mechanical property testing and metallographic evaluation. Personally, I would rather just print some and pressurize them until they blew up, but my graduate student and I tried that and maxed out the pressure in the test rig in Penn State’s High Pressure Combustion Lab (thanks David Drewniak for your help testing and SLM Solutions for printing test samples for us). We saw no sign of deformation even at 2.5 times the rated load; so, I guess we accidently overdesigned the AM pressure vessel when we modified the shell’s interior to eliminate support structures. I wish we had had ASME’s standard earlier — or the support-free AM capability I discussed last month!
Related Content
Digital Thread Enables First-Time-Right 3D Printing
Connecting all stages of manufacturing, from design to postprocessing, helps break down barriers to industrializing additive manufacturing.
Read MoreHow Automation Keeps Quality Control in Control
Collaborative robots help inspection keep pace with machining in a custom, digitalized workflow for complex aerospace and defense parts.
Read MoreGo Digital: How to Succeed in the Fourth Industrial Revolution With Additive Manufacturing
The digitalization of manufacturing is set to transform production and global supply chains as we know them, and additive manufacturing has been leading the way in many industries.
Read MoreView From My Shop, Episode 2: 3D Printing and Postprocessing With Tangible Solutions
Collaboration between Tangible Solutions’ additive and machining departments simplifies their work. Learn more in this episode of The View From My Shop.
Read MoreRead Next
The Cut Scene: The Finer Details of Large-Format Machining
Small details and features can have an outsized impact on large parts, such as Barbco’s collapsible utility drill head.
Read MoreObscure CNC Features That Can Help (or Hurt) You
You cannot begin to take advantage of an available feature if you do not know it exists. Conversely, you will not know how to avoid CNC features that may be detrimental to your process.
Read More3 Mistakes That Cause CNC Programs to Fail
Despite enhancements to manufacturing technology, there are still issues today that can cause programs to fail. These failures can cause lost time, scrapped parts, damaged machines and even injured operators.
Read More