Latest MachineWorks Update Improves Simulation Performance
MachineWorks 8.4 includes enhanced APIs, improved cimulation performance through collision check buffing, enhanced analysis of intersect solids for bending simulation and more.
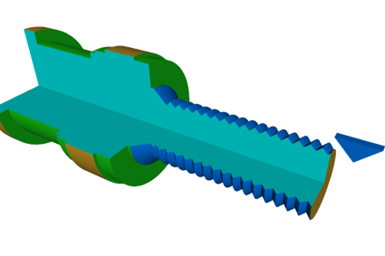
MachineWorks Ltd, a supplier of software components to the engineering industry, has released an updated version of its software, MachineWorks 8.4 with a number of new features.
The collision check buffering feature was designed to improve simulation performance. This option allows computation of collision checking to be deferred until required by the host application, which can speed tool and holder collision checks in cases where no material is being removed. This option also significantly improves performance for CMM and metrology inspection applications.
Another added feature is the computation of safe holder profiles: Applications can determine the maximum safe profile which can be used to machine a particular toolpath without collisions. The resulting holder profile can then be compared with available holders in a tool library so the user can choose a holder that won’t cause collisions during cutting.
A function has been added to compute multiple, simultaneous collision checks between tools and holders and/or stocks and fixtures. The function is internally multithreaded to support toolpath generation and optimization algorithms, along with rapid path evaluation for CMM and metrology inspection plans.
MachineWorks says its Render Query APIs have been expanded, particularly with respect to analyzing design part or target part comparison results. The Render Query APIs provide an optimized mechanism to decouple the graphical simulation from the geometric simulation, allowing integration of the software to external graphics environments or use in distributed deployments, such as public and private clouds.
Cut numbers are now available in render query updates. The APIs allow the Render Query analysis mesh to be serialized to disk, and additional filters are provided to specify which triangles are delivered by the Render Query update. A new API to provide direct export of analysis mesh distance information has also been provided. This facilitates, for example, creation of polycurves representing boundaries between different material depths.
Other notable enhancements include improved analysis of intersect solids for bending simulation, sectioned stock view and application-defined swept volumes.