New Metalworking Products from Modern Machine Shop, Dec. 06, 2019
The latest technology from Kitamura Machinery of USA, Olympus, Mitsui Seiki (USA), German Machine Tools of America, and The L.S. Starrett Co.
Kitamura's Mycenter-HX300iG 400 Combines Large Work Area in Small Footprint
Kitamura Machinery’s Mycenter-HX300iG/400 expands the company’s small-footprint HMC offering, providing heavy-duty cutting, accuracy and reliability.
Kitamura Machinery’s Mycenter-HX300iG/400 expands the company’s small-footprint HMC offering, providing heavy-duty cutting, accuracy and reliability. For its size, the machine is still designed with a large work envelope, with a maximum workpiece diameter of 500 mm (19.7"), a maximum workpiece height of 745 mm (29.3"), and XYZ axes measuring 460 × 510 × 560 mm (18.1" × 20.1" × 22"), respectively. A 400-mm table option offers additional workholding possibilities.
The 30-hp, 15,000-rpm, 40-taper, direct-drive, dual-contact spindle is said to be capable of handling a variety of exotic materials. A 20,000-rpm dual contact spindle is also available.
The fully integrated fourth-axis rotary table, equipped with an integral drive motor, enables rapid indexing speeds of 150 rpm (54,000 degrees per min.) reducing out-of-cut time, eliminating backlash and providing positioning accuracy of ±2 arcseconds.
An expandable 50-tool automatic toolchanger allows for the addition of up to 200 tools as needs change. The ATC is fixed-pot, which ensures that tools are always returned to the same pot and that the next tool to be used is kept in a stand-by pot) A 1.3-sec. tool-change time contributes to the reduction in overall cycle time made possible by the machine, the company says.
The Mycenter-HX300iG/400 provides positioning accuracy of ±0.002 mm (±0.000079") with 67-million-pulse encoder technology for better finish accuracy. To accommodate a variety of metal cutting requirements, the machine offers rapid traverse rates of 60 m/min. (2,362 ipm), ballscrew cooling, and 10-nm optical linear scale feedback in the linear axes.
Lightweight Vanta Element Analyzes Metal Alloy Grades
The Vanta Element X-ray fluorescence (XRF) analyzer from Olympus is designed as a cost-effective model that still provides speed, reliability, connectivity and ease of use.
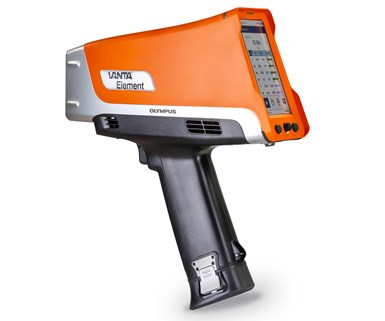
The Vanta Element X-ray fluorescence (XRF) analyzer from Olympus is designed as a cost-effective model that still provides speed, reliability, connectivity and ease of use. The analyzer can obtain clear material and grade ID and compare alloy grades on the instrument’s screen. With a dual-core processor powered by Olympus’ Axon technology, the lightweight Vanta Element has the same stability and resolution as the rest of the Vanta series.
Built for use in demanding environments, the Vanta Element is IP54-rated for resistance to dust and moisture and constructed to pass a 4-ft. drop test (MIL-STD-810G). For additional protection, a stainless steel faceplate is paired with a thick (50-micron) Kapton window that can be easily attached and removed for window changes on the shop floor. The device can perform continuously in environmental temperatures ranging from 14°F to 113°F (-10°C to 45°C).
The analyzer can connect to the Olympus Scientific Cloud for wireless data sharing and access to fleet management tools like the Olympus mobile app. The analyzer also has an industrial 1-GB MicroSD card for storing results and two USB ports for data export. For added flexibility, the Vanta Element analyzer is compatible with accessories including the Vanta field stand, soil foot, probe shield and holster.
Mitsui Seiki's J350G Jig Grinder Enables Various Operations Without Wheel Change
The Mitsui Seiki J350G jig grinder is designed to provide a combination of application flexibility, accuracy and user-friendly operation.

The Mitsui Seiki J350G jig grinder is designed to provide a combination of application flexibility, accuracy and user-friendly operation. The machine has a long grinding infeed stroke, with a U-axis range of -3 to +50 mm relative to the spindle center. This is said to provide the flexibility to grind small- and large-diameter holes, as well as multiple features, using a single wheel in a continuous, automatic mode.
According to Tom Dolan, vice president of sales and marketing, “The J350G jig grinder gives users the ability to grind a wide variety of features automatically, without changing wheels. It thereby provides the flexibility required in today’s manufacturing environment.”
To maximize accuracy, the hand-scraped X and Y axes of the J350G incorporate needle roller bearings. The machine bed consists of a thick, rigid casting supported by three level points, providing consistent perpendicularity and parallelism. Built-in, custom-designed Heidenhain scales contribute to ±0.0007 mm accuracy on the X, Y and Z axes, the company says.
The machine’s X-, Y- and Z-axis travels measure 500 × 300 × 100 mm, respectively. The maximum distance from the table surface to the grinding spindle nose is 450 mm. The work surface measures 700 × 350 mm, with a permissible table load of 300 kg. Table and saddle maximum rapid feed rates range to 2,000 mm/min., while grinding feed rates are variable from 0.1 to 2,000 mm/min. The standard high-frequency spindle motor operates from 9,000 to 45,000 rpm. A variety of spindle motor options include an air-turbine motor with 75,000-rpm capability.
The FANUC 31i-B control has a 15" LCD touchscreen and is preloaded with G-MAPS conversational-style programming software. The control is said to ease manual programming with graphic icons, data entry or conventional methods.
Profilator S Machines Capable of Various Gear Machining Operations
GMTA, the North American distributor of Profilator, has added S-type machines using the process modules it already supplies.

GMTA, the North American distributor of Profilator, has added S-type machines using the process modules it already supplies. The Profilator can perform polygon and face slot machining, geartooth pointing, chamfering and deburring, gear and spline cutting, shifter stop machining, and scudding.
The twin-spindle S-type is a modularly designed, vertical pick-up gear cutting machine. Most applications on the machine use a dry machining process. All machine components are designed for high static stiffness and optimal dynamic behavior. A control panel and media container are installed on the rear of the machine bed. The workplace flow direction is variable.
S-series machines are available in three sizes: S-150, S-250 and S-500. These models accommodate part diameters ranging to 150, 250 and 500 mm, respectively.
The polygon turning unit is used for castle teeth machining on automotive gearbox parts. The rotating cutter head is synchronized with the workplace spindle for front-face coupling with the carbide insert arrangement and the transmission ratio. With additional inserts on the same cutter head, the part can also be deburred. In gear tooth pointing applications, the pointing tower can be used in both rotative and indexing modes. Settings and corrections are made through the Ergo Control SIMPS (Profilator Simplified Integrated Machine Programming System). The shifter stop is synchronized so that the tool machines each tooth flank. Lastly, the machine can perform the scudding process for a range of symmetrical gear applications as well as non-symmetrical gear or profile applications such as belt pulleys and synchronize gears. The same machine can be used for internal and external scudding operations.
L.S. Starrett Adds Rockwell, Vickers and Brinell Hardness Testers
The L.S. Starrett Co. has expanded its series of benchtop hardness testers with seven Rockwell systems, eight Vickers systems and one Brinell system.

The L.S. Starrett Co. has expanded its series of benchtop hardness testers with seven Rockwell systems, eight Vickers systems and one Brinell system.
The Rockwell additions include two regular Rockwell digital testers, two superficial Rockwell testers (one dial and one digital), two twin Rockwell-superficial testers (one dial and one digital), and two Twin Rockwell-Superficial testers with a dolphin-nose design. The dolphin-nose systems are fully automated with output to a PC and the capability of measuring 30 different Rockwell scales.
The new Vickers hardness testers include six micro Vickers testers for handling a testing range of 1HV to 2967HC and eight test forces; two with Digicam Basic Manual software for manually selecting edges of indentation; two with Digicam Auto software for automatically detecting edges of indentation; and two testers with Auto Turret Control (one with Basic software, one with Auto software). In addition, there are two macro Vickers testers for handling up to 17 test forces; one features Digicam Basic Manual software and one featuring Digicam Automatic Software.
The Starrett digital Brinell hardness tester features automatic loading and can handle 10 scales.
Read Next
The Cut Scene: The Finer Details of Large-Format Machining
Small details and features can have an outsized impact on large parts, such as Barbco’s collapsible utility drill head.
Read More3 Mistakes That Cause CNC Programs to Fail
Despite enhancements to manufacturing technology, there are still issues today that can cause programs to fail. These failures can cause lost time, scrapped parts, damaged machines and even injured operators.
Read More