Sandvik Coromant and Autodesk Partner for Increased Utility
Sandvik Coromant and Autodesk have partnered to solve issues in CAM. Their first solution is to present Sandvik Coromant tool data within Autodesk Fusion 360.
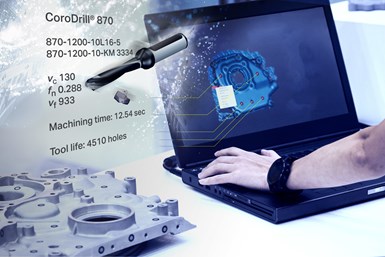
Sandvik Coromant has announced a new partnership with Autodesk, marking the brands’ plans to advance the future of Computer-Aided Manufacturing (CAM). The first step of the collaboration will tackle the complex task of specifying cutting tools to determine the most effective way to use them. In this step, the companies will streamline data selection by providing Autodesk Fusion 360 users with access to Sandvik Coromant tool data.
“Today’s manufacturing world is increasingly competitive,” says Jonas Ström, product manager at Sandvik Coromant. “Materials are lighter, harder and stronger; machines are more advanced; batch sizes are smaller; and component design is increasingly complex – all of this leads to an increased need for CAM programming and skilled CAM users.
“As engineers, CAM users love seeking new technologies and testing solutions, but they are often limited by the time constraints associated with CNC machining,” continues Ström. “By providing them access to tool information, recommendations and knowledge of unique machining methods at the click of a button, we hope to simplify their process.”
Typically, CAM users rely on manually transferring data from tooling catalogues and inputting the parameters into CAM software. This process is often laborious and can increase time-to-market expectations.
“Manufacturing and metal cutting are already complex processes, and they’re often made more difficult by manually managing tooling information, resulting in delayed setup times and increased room for machining error,” says Srinath Jonnalagadda, vice president of business strategy for Design and Manufacturing at Autodesk. “By pairing our CAM software solutions with Sandvik Coromant’s deep tooling knowledge and expertise, we’re helping customers reduce time and improve efficiency in the preparation phase.”
Related Content
-
TTI Brings Specialty Gear Production In-House with Multiaxis Machining
By investing in a 3+2-axis machine and utilizing simulation software for diagnostic checks, Techtronic Industries turned a four- to ten-week lead time into a one- to two-week lead time.
-
How Integrated CAD/CAM Transforms Inventions Into Products
The close connection between CAD and CAM is what links creative ideas to practical production for this unique custom manufacturer.
-
When to Use Custom Macros With a CAM System
Custom macros can offer benefits even when using a CAM system to prepare programs – but must be implemented with the right considerations.