Siemens Upgrades CNC Operating Software Solutions
Sinumerik CNC software release 4.8 is designed to improve the speed, precision and safety of intermediate milling, turning and grinding machine tools, with simplified ISO code programming.
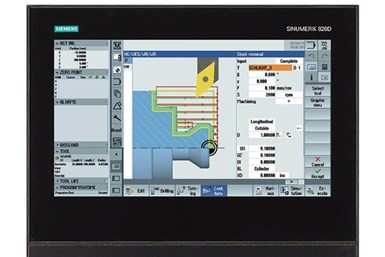
Siemens has released of version 4.8 of its operating software, which features an array of new hardware and software solutions for its integrated Sinumerik portfolio. The offering comprises integrated industrial software and automation technology designed to enable machine tool manufacturers to leverage the full productivity potential of the digital factory in a mid-range control.
With its new Sinumerik CNC software release 4.8, Siemens is making a range of new functions available to improve the speed, precision and safety of intermediate milling, turning and grinding machine tools, with simplified ISO code programming. Features of version 4.8 include facility for compensating unwanted axis nodding movements and protection against machine, tool and workpiece collisions. Nodding compensation (NoCo) is used to compensate for dynamic position deviations in one or more linear machine axes caused by acceleration processes. These position deviations are caused by what is known as mechanical compliance within the machine. NoCo compensates for the dominant position deviation by initiating a corrective movement in the relevant machine axis, enabling improved machining quality simultaneously with higher jerk and acceleration values. Nodding compensation can reportedly be used in conjunction with any technology, such as milling, multi-tasking, tapping, laser machining or waterjet machining. NoCo is available in two variants: Eco and Advanced. The Eco variant is designed for dominant acceleration effects in which the compensation axis is combined with one influencing variable. The Advanced variant is designed for operations where there are several influencing variables that require several compensation axes.
Related Content
-
Understanding CNC Machine Accuracy and Repeatability
Properly evaluating machine tool capability requires understanding how the both user and the builder can influence precision.
-
Understanding G27, G28, G29 and G30
Take a closer look at these reference position commands.
-
Five Safety Considerations for CNC Machinists
Safety in CNC environments is essential for users – and for productivity. Consider these 5 points to avoid injury, part failure and downtime.