4 Ways Eastec Evidenced Manufacturing’s Evolution
From tooling and workholding to Industry 4.0, the pursuit of new CNC machining opportunity united all who turned out for the 2021 event.
Whatever “normal” will look like for industry events remains to be seen, but one thing is certain: there’s no replacement for face-to-face interaction.
Just ask anyone who attended Eastec 2021, the largest metalworking trade show in the Northeast, October 19-21 in Springfield, Mass. However the numbers compare to past or future events, the crowd was more than robust enough and the quality of the interaction was more than high enough for Eastec to feel like a trade show should feel.
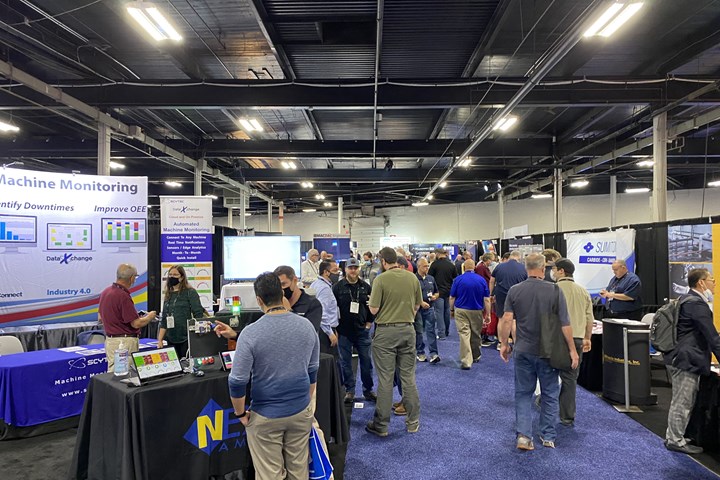
Attendees roam the halls of “The Big E,” or the Eastern States Exposition, at Eastec 2021.
With so many movers and shakers face-to-face and in one place, Eastec also proved ideal for drawing a few broad conclusions about how digitalization, automation and even new business practices are changing our industry. Here are four examples:
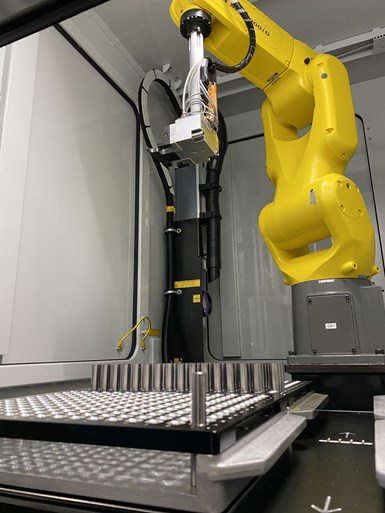
Exhibitors with multi-disciplinary expertise and robust support networks were eager to trumpet their advantages. For example, Anca highlighted its capabilities for near-complete automation of the tool-grinding process, ranging from integrated robots to workholding to its new AutoMark X laser marking machine. As shown here, the system uses a robot to manipulate cutting tools (or any other cylindrical parts) around the laser.
1. Change is holistic. Robots and other physical automation was plentiful, but shops’ plans can extend well beyond the shop floor. For example, two rather large, competing and adjacent booths touted software to automate the ballooning of drawings and the generation of quality control documentation, among other capabilities.
2. Process control is getting easier. Holistic thinking is required in part because automation, as well as data and the sensors that collect it, are virtually ubiquitous. Consider the zero-point workholding system below, which uses pneumatics to verify proper workpiece seating. The analog or digital sensor that reads the pressure might be tied into a PLC or control system as part of an automation solution or, potentially, used to track cycles or the number of times a device is actuated.
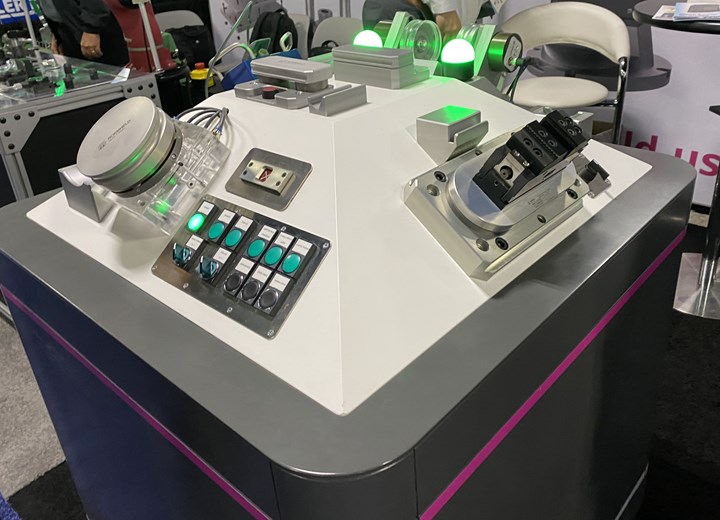
In this demonstration from Carr Lane Manufacturing Co, visual feedback from pneumatic pressure sensors indicates whether clamps tighten or release correctly.
3. The data are there for the taking. There was no shortage of machine monitoring software at Eastec. Some had big news to report. Others reported good business. Many also emphasized the low barrier of entry to machine monitoring.
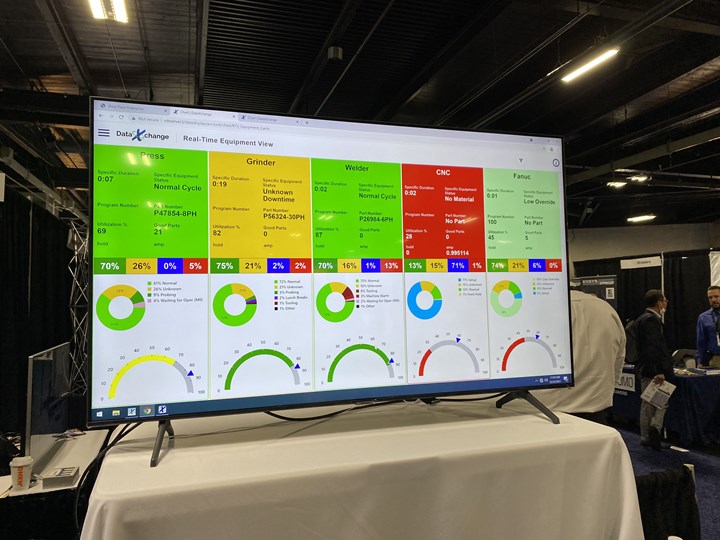
Scytec, developer of the DataXChange monitoring system, reported that business has been strong in part due to recent workforce and supply chain disruptions. Machine monitoring can help by providing information that schedulers and other personnel can use to allocate resources as needed, when needed.
However, what was perhaps the most direct example of low barrier to entry when it comes to the Industrial Internet of Things (IIoT) was highlighted by a nonprofit, Advanced Manufacturing International (AMI). Called the Low Investment Manufacturing Solution (LIMS), the system is intended to be just that — a plug-and-play “gateway” to IIoT that is easy to implement and easy to scale.
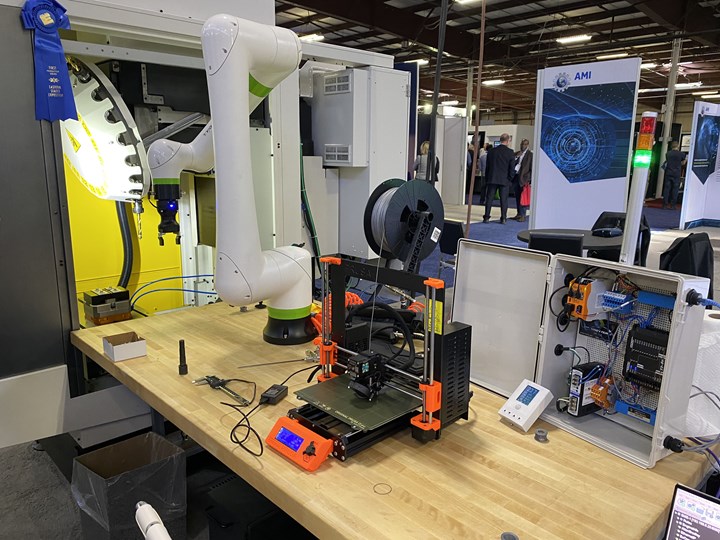
In this demonstration, the LIMS system from AMI links mulitiple, different pieces of equipment, including a 3D printer, which prints the part; a collaborative robot; and the VMC, which automatically queues up the right-sized drill to enlarge the hole based on caliper measurements.
4. Challenge and opportunity abound. The presence of less traditional exhibitors — including some making their metalworking trade show debut — also spoke to the kinds of change attendees are experiencing back at their shops. For example, Steel Root specializes in cybersecurity. The company sees particular opportunity in manufacturing due to upcoming requirements such as new cybersecurity maturity model certification (CMMC). S&G is an accounting and consulting firm eager to help shop leaders with business transitions, including shop sales and generational change.
Read Next
The Cut Scene: The Finer Details of Large-Format Machining
Small details and features can have an outsized impact on large parts, such as Barbco’s collapsible utility drill head.
Read MoreObscure CNC Features That Can Help (or Hurt) You
You cannot begin to take advantage of an available feature if you do not know it exists. Conversely, you will not know how to avoid CNC features that may be detrimental to your process.
Read More3 Mistakes That Cause CNC Programs to Fail
Despite enhancements to manufacturing technology, there are still issues today that can cause programs to fail. These failures can cause lost time, scrapped parts, damaged machines and even injured operators.
Read More