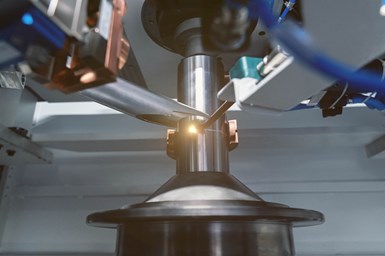
During the welding process on the ELC 6, the vertically arranged workpiece rotates. The precisely meterable energy of the laser beam allows a high welding speed. (Photo credits: Emag LLC)
Rotor shafts are key components for electric vehicle (EV) motors. Automotive production planners continuously focus their efforts on establishing effective design and manufacturing processes to produce them.
Hollow components provide design freedom, less weight and lower material costs for assembled rotor shafts. Still, this “heart” of an electric motor must withstand particularly high loads as motor speeds as high as 20,000 rpm are now possible. Compared to a camshaft in an internal combustion engine, for example, this value is many times higher. Thus, the production of assembled rotor shafts is always about manufacturing tolerance because even minimal imbalances must be avoided at all costs because they could reduce motor life.
Emag LaserTec offers an automated solution to “build” two-piece rotor shafts to support the growing EV market based on its Emag Laser Cell (ELC 6) laser welding machine. In addition to the machine, the process includes part handling, preheating and joining as well as a rotary table to enable timed welding operations to take place in fast succession.
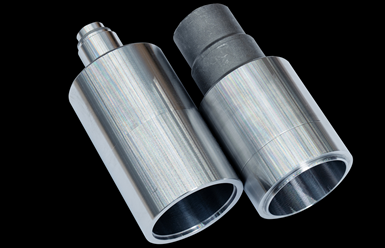
For rotor shafts, hollow components provide less weight and lower material costs.
The precisely metered, concentrated energy of the laser beam permits high welding speeds with minimal distortion on the welded component, the company says. A look at the details reveals the performance of the machine, which was specially developed for powertrain components with circumferential welds:
- Before the individual parts are loaded into the ELC 6, the workpieces are cleaned using a laser. For this purpose, Emag LaserTec offers the LC 4 laser cleaning machine, which can be optimally link with the ELC 6 to offer seamless line integration.
- Preheating and joining occur in the next step in the ELC 6. The induction technology first ensures an optimal processing temperature on the component before the two components are joined.
- Before welding, the weld seam position is verified and the component position is readjusted as necessary. The contour is scanned and the data is communicated to the welding optics and the NC axes.
- During the subsequent welding process, the vertically arranged workpiece rotates, while the laser optics move only radially towards the workpiece. The welding process with its focused energy thus takes place virtually from the side at the circumferential weld. A pyrometer controls the process temperature.
- After welding, the component is transported out of the machine by a swiveling motion of the rotary table and unloaded by a robot.
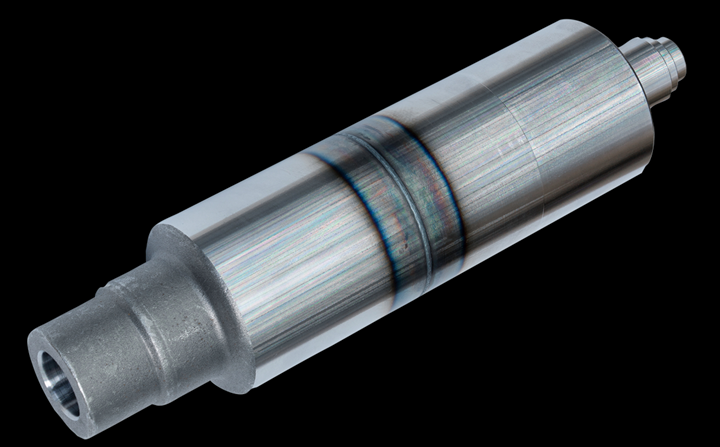
This rotor shaft design provides developers a great deal of design freedom.
Overall, this solution provides high production speed in part because the machine with its rotary table is loaded and unloaded during welding (and is thus cycle time-concurrent). In addition, the individual subprocesses are synchronized. The “fixed optics/moving workpiece” principle was created to help ensure a high level of operational reliability. In addition, Emag LaserTec designs this solution very flexibly for customers in terms of technology, output and automation, whereby workpieces with a maximum height and external of 300 millimeters can be welded in the ELC 6.
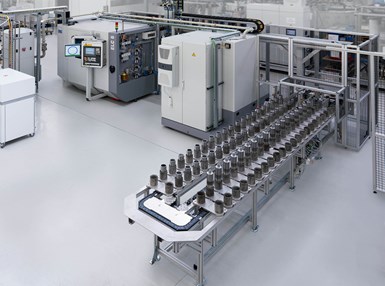
The ELC 6 was specially developed for automated, high-volume production of rotor shafts for EV motors.
Emag has also developed related solutions such as the subsequent joining of the rotor shaft and rotor-sheet package as well as precision overturning of this package. The same applies to the turning, gear cutting and grinding of the two individual rotor shaft parts before welding.
When it comes to the automation technology for effective transport between the machines, the company says it adapts to its customers’ ideas. For example, line gantries, stacking cells, accumulating conveyors or its own TrackMotion system can be used. These systems benefit from the uniformity of the machines used with their optimized interfaces. And, as a result, Emag says it is the only contact required during planning, implementation and servicing.
Related Content
Ford Partners With Rockwell Automation to Advance EV Program
The companies will jointly collaborate on assembly tooling designs and architectures that will increase speed to market.
Read MoreElectric Vehicles Spark Bright Ideas
Ford alone expects to have production capacity for 600,000 electric vehicles by late 2023, and more than 2 million by the end of 2026. The effects on manufacturing are BIG.
Read MoreDN Solutions Responds to Labor Shortages, Reshoring, the Automotive Industry and More
At its first in-person DIMF since 2019, DN Solutions showcased a range of new technologies, from automation to machine tools to software. President WJ Kim explains how these products are responses to changes within the company and the manufacturing industry as a whole.
Read MoreSiemens and Mahle Partner to Develop Wireless EV Charging
Mahle will contribute its experience as an automotive supplier and Siemens will use its expertise in the field of charging infrastructure to develop wireless charging stations for electric vehicles.
Read MoreRead Next
Obscure CNC Features That Can Help (or Hurt) You
You cannot begin to take advantage of an available feature if you do not know it exists. Conversely, you will not know how to avoid CNC features that may be detrimental to your process.
Read MoreThe Cut Scene: The Finer Details of Large-Format Machining
Small details and features can have an outsized impact on large parts, such as Barbco’s collapsible utility drill head.
Read More3 Mistakes That Cause CNC Programs to Fail
Despite enhancements to manufacturing technology, there are still issues today that can cause programs to fail. These failures can cause lost time, scrapped parts, damaged machines and even injured operators.
Read More